Work Practice Control Definition
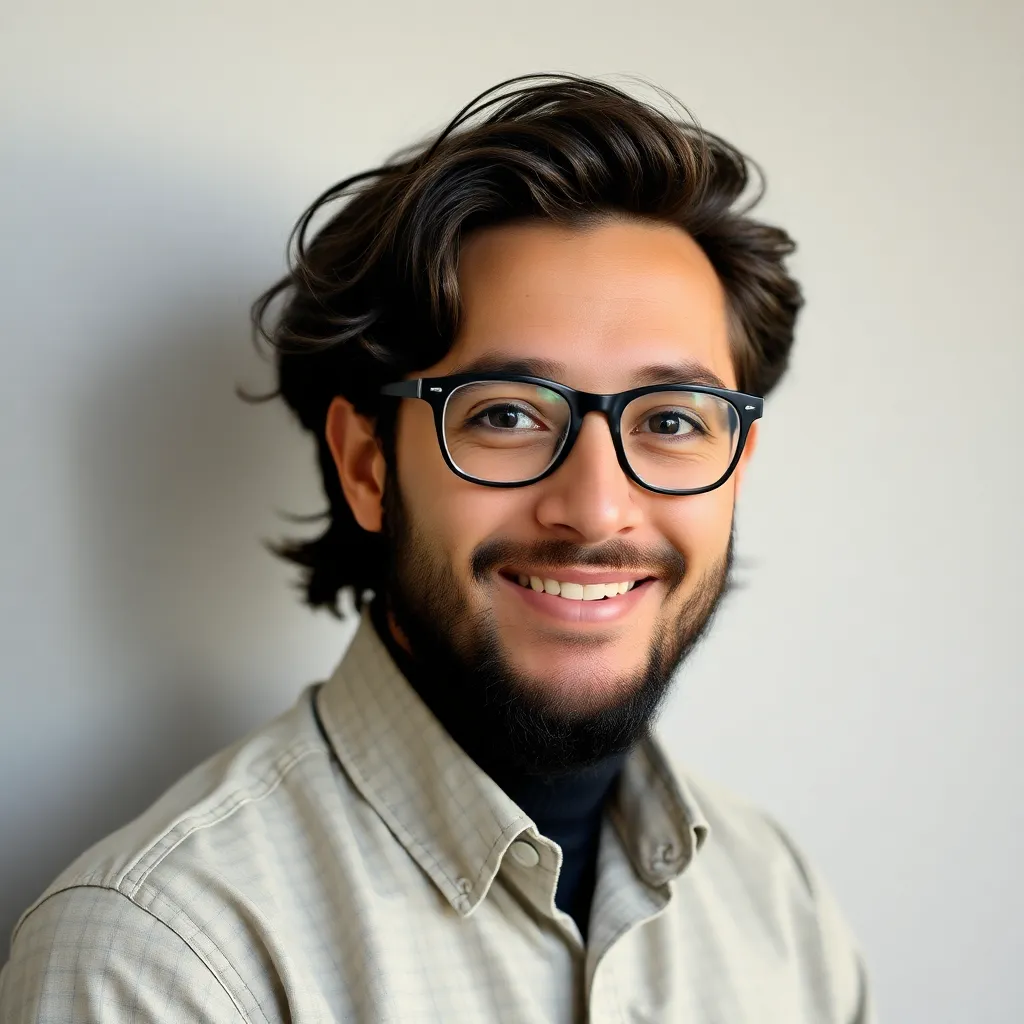
adminse
Apr 01, 2025 · 9 min read
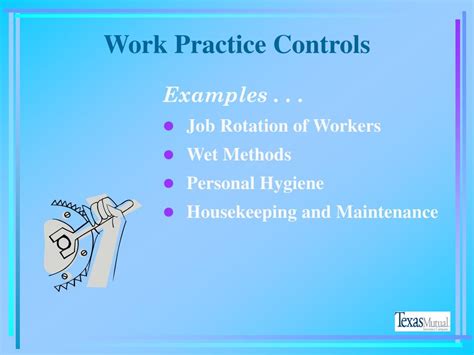
Table of Contents
Mastering the Art of Work Practice Control: A Comprehensive Guide
What if the future of workplace safety and efficiency hinges on a robust understanding of work practice controls? This critical element is the backbone of a thriving and secure work environment, minimizing risks and maximizing productivity.
Editor’s Note: This article on work practice control definitions, implementation, and best practices has been published today, offering readers the latest insights into this crucial aspect of workplace management.
Why Work Practice Control Matters:
Work practice controls are the unseen guardians of a productive and safe workplace. They are not about physical barriers or equipment modifications, but rather about the consistent and safe execution of tasks. This encompasses everything from proper handwashing techniques in a healthcare setting to the correct lifting procedures in a warehouse. Their importance stems from their ability to:
- Reduce workplace accidents and injuries: By standardizing procedures and training employees in safe work practices, the likelihood of errors and resulting incidents decreases significantly.
- Improve operational efficiency: Well-defined work practices streamline processes, minimizing wasted time and resources. Consistency in approach leads to better quality output and reduced rework.
- Enhance product quality: Consistent work practices ensure products and services meet quality standards, reducing defects and customer complaints.
- Boost employee morale and engagement: Employees feel safer and more valued when they know clear procedures are in place and they're trained properly. This leads to increased engagement and productivity.
- Meet regulatory compliance: Many industries have strict regulations regarding safety and work practices. Implementing and maintaining effective controls ensures compliance and avoids penalties.
Overview: What This Article Covers
This article provides a comprehensive exploration of work practice controls. It delves into the precise definition, different types, implementation strategies, challenges, and the crucial role of training. Readers will gain a practical understanding of how to develop and maintain effective work practice controls, ultimately creating a safer and more productive workplace.
The Research and Effort Behind the Insights
This article is the result of extensive research, drawing upon industry best practices, safety regulations (OSHA, NIOSH, etc.), and case studies illustrating both successful implementations and common pitfalls. The information presented is supported by evidence-based research and aims to provide readers with accurate and actionable insights.
Key Takeaways:
- Definition and Core Concepts: A clear understanding of what constitutes work practice controls and their foundational principles.
- Types of Work Practice Controls: Identifying the various categories of work practice controls and their applications.
- Implementation Strategies: A step-by-step guide to developing and implementing effective work practice controls.
- Training and Communication: The importance of comprehensive employee training and consistent communication.
- Challenges and Solutions: Addressing common obstacles in implementing and maintaining work practice controls.
- Monitoring and Evaluation: Strategies for continuous improvement and ensuring the effectiveness of controls.
- The Role of Technology: Exploring how technology can enhance work practice control systems.
Smooth Transition to the Core Discussion:
Having established the significance of work practice controls, let's delve into a detailed examination of their definition, types, and implementation.
Exploring the Key Aspects of Work Practice Control
1. Definition and Core Concepts:
Work practice control refers to a set of standardized procedures and techniques designed to reduce or eliminate workplace hazards by modifying the way a task is performed. Unlike engineering controls (modifying equipment or the workplace) or administrative controls (changing work schedules or policies), work practice controls focus on human behavior and task execution. They are proactive measures aimed at preventing accidents and injuries before they happen. Key aspects include:
- Standardization: Consistent performance of tasks to minimize variability and errors.
- Training: Thorough instruction and practice to ensure employees understand and can apply the procedures.
- Supervision: Regular monitoring to ensure compliance and identify areas for improvement.
- Documentation: Recording procedures, training records, and monitoring data for traceability and accountability.
2. Types of Work Practice Controls:
Work practice controls are not one-size-fits-all. They are tailored to specific tasks and hazards. Some common types include:
- Safe Operating Procedures (SOPs): Step-by-step instructions for operating equipment or performing specific tasks.
- Lockout/Tagout Procedures: Methods to isolate energy sources to prevent accidental starts during maintenance or repairs.
- Personal Protective Equipment (PPE) Use: Correct selection, donning, and doffing of PPE to protect employees from hazards.
- Ergonomic Practices: Techniques to reduce physical strain during repetitive tasks or when handling heavy objects.
- Housekeeping Practices: Maintaining a clean and organized work environment to minimize slips, trips, and falls.
- Hygiene Practices: Procedures to prevent the spread of contamination or infection (relevant in healthcare, food processing, etc.).
3. Implementation Strategies:
Effective implementation requires a systematic approach:
- Hazard Identification and Risk Assessment: Identify potential hazards and assess the risks associated with each task.
- Procedure Development: Create clear, concise, and easy-to-understand procedures for each task. Use visuals (flowcharts, diagrams) where appropriate.
- Employee Training: Provide thorough training on all procedures, including hands-on practice and competency assessments.
- Supervision and Monitoring: Regularly supervise employees to ensure compliance and identify any deviations from procedures.
- Documentation: Maintain records of procedures, training, and monitoring activities.
- Continuous Improvement: Regularly review and update procedures based on feedback, incidents, and changes in technology or regulations.
4. Training and Communication:
Effective training is crucial. It shouldn't just be a one-time event; it should be ongoing and reinforced through:
- Interactive Training: Hands-on practice, simulations, and group discussions to enhance learning and retention.
- Regular Refresher Training: Periodic training sessions to reinforce procedures and address any changes.
- Clear Communication: Establish clear communication channels to address employee questions and concerns.
- Feedback Mechanisms: Encourage employees to provide feedback on procedures and identify areas for improvement.
5. Challenges and Solutions:
Implementing effective work practice controls can face challenges:
- Resistance to Change: Employees may be resistant to new procedures. Address concerns proactively and involve employees in the development process.
- Lack of Resources: Insufficient time, funding, or personnel can hinder implementation. Prioritize high-risk tasks and allocate resources effectively.
- Inadequate Training: Poorly designed or delivered training can lead to ineffective implementation. Use a variety of training methods and ensure competency assessments.
- Inconsistency in Enforcement: Lack of consistent monitoring and enforcement can undermine the effectiveness of controls. Establish clear accountability and consequences for non-compliance.
6. Monitoring and Evaluation:
Regular monitoring and evaluation are crucial to ensure the effectiveness of work practice controls:
- Regular Audits: Conduct regular audits to assess compliance with procedures.
- Incident Reporting: Establish a system for reporting and investigating workplace incidents.
- Performance Indicators: Track key performance indicators (KPIs) to measure the effectiveness of controls.
- Data Analysis: Analyze data to identify trends and areas for improvement.
7. The Role of Technology:
Technology plays an increasingly important role in enhancing work practice controls:
- Digital SOPs: Providing access to procedures through mobile devices or digital platforms.
- Real-time Monitoring: Using sensors and data analytics to monitor employee performance and identify potential hazards.
- Virtual Reality Training: Providing immersive training experiences to enhance learning and retention.
- Automated Safety Systems: Implementing automated systems to prevent errors and improve safety.
Closing Insights: Summarizing the Core Discussion
Work practice controls are not merely a checklist; they are a fundamental element of a safe and productive workplace. By understanding the principles, implementing strategies, and embracing continuous improvement, organizations can significantly reduce risks, enhance efficiency, and foster a positive work environment.
Exploring the Connection Between Training and Work Practice Control
Training is inextricably linked to the success of work practice controls. It's the bridge between well-defined procedures and their consistent application by employees. Without effective training, even the most meticulously crafted procedures remain ineffective.
Key Factors to Consider:
-
Roles and Real-World Examples: Effective training programs consider the specific roles and responsibilities of employees, tailoring the content to their needs. For example, a warehouse worker’s training on safe lifting techniques differs greatly from a nurse's training on infection control protocols.
-
Risks and Mitigations: Poor training leads to incorrect practices, increasing the risk of accidents and injuries. Mitigating this risk requires comprehensive training, regular refresher courses, and competency assessments.
-
Impact and Implications: The impact of effective training extends beyond immediate safety concerns. It contributes to increased productivity, improved quality, reduced waste, and higher employee morale. Conversely, inadequate training can lead to increased costs due to accidents, rework, and low employee satisfaction.
Conclusion: Reinforcing the Connection
The connection between training and work practice controls is paramount. Investing in comprehensive and well-designed training programs is not an expense; it's a strategic investment that safeguards employee well-being, boosts productivity, and promotes a culture of safety and continuous improvement.
Further Analysis: Examining Training Methods in Greater Detail
Effective training leverages diverse methods:
- On-the-Job Training (OJT): Learning by doing, under the supervision of experienced colleagues.
- Classroom Training: Formal instruction using lectures, presentations, and discussions.
- Simulation Training: Replicating real-world scenarios to practice procedures in a safe environment.
- E-Learning: Online modules and interactive exercises for convenient and self-paced learning.
- Blended Learning: Combining multiple methods for a comprehensive learning experience.
FAQ Section: Answering Common Questions About Work Practice Control
-
What is the difference between work practice controls and engineering controls? Engineering controls modify the workplace or equipment to reduce hazards, while work practice controls focus on how tasks are performed.
-
How often should work practice controls be reviewed and updated? Regularly, at least annually, or more frequently if there are significant changes in processes, technology, or regulatory requirements.
-
What are the legal implications of failing to implement adequate work practice controls? Failure to implement adequate controls can result in penalties, fines, and legal action, especially in industries with strict safety regulations.
-
How can I measure the effectiveness of my work practice control program? Track key performance indicators such as accident rates, near-miss incidents, and employee feedback.
-
What resources are available to help implement work practice controls? OSHA, NIOSH, and other industry organizations offer guidelines, training materials, and resources.
Practical Tips: Maximizing the Benefits of Work Practice Control
-
Start with a thorough hazard identification and risk assessment.
-
Involve employees in the development and implementation of work practice controls.
-
Use clear, concise, and easy-to-understand language in procedures.
-
Provide comprehensive training and ongoing support.
-
Monitor and evaluate the effectiveness of controls regularly.
Final Conclusion: Wrapping Up with Lasting Insights
Work practice control is not just a matter of compliance; it's a fundamental strategy for creating a safe, efficient, and productive work environment. By understanding the principles, implementing the strategies, and fostering a culture of safety and continuous improvement, organizations can achieve a level of workplace excellence that benefits both employees and the bottom line. The proactive approach of work practice control ultimately results in a more resilient, adaptable, and successful organization.
Latest Posts
Latest Posts
-
How To Calculate Late Fee In Gst
Apr 03, 2025
-
How To Check Late Fee In Gst Portal
Apr 03, 2025
-
How To Calculate Late Fees On Invoices
Apr 03, 2025
-
What Is The Late Payment
Apr 03, 2025
-
What Is The Late Fee
Apr 03, 2025
Related Post
Thank you for visiting our website which covers about Work Practice Control Definition . We hope the information provided has been useful to you. Feel free to contact us if you have any questions or need further assistance. See you next time and don't miss to bookmark.