What Is Mrp In Supply Chain
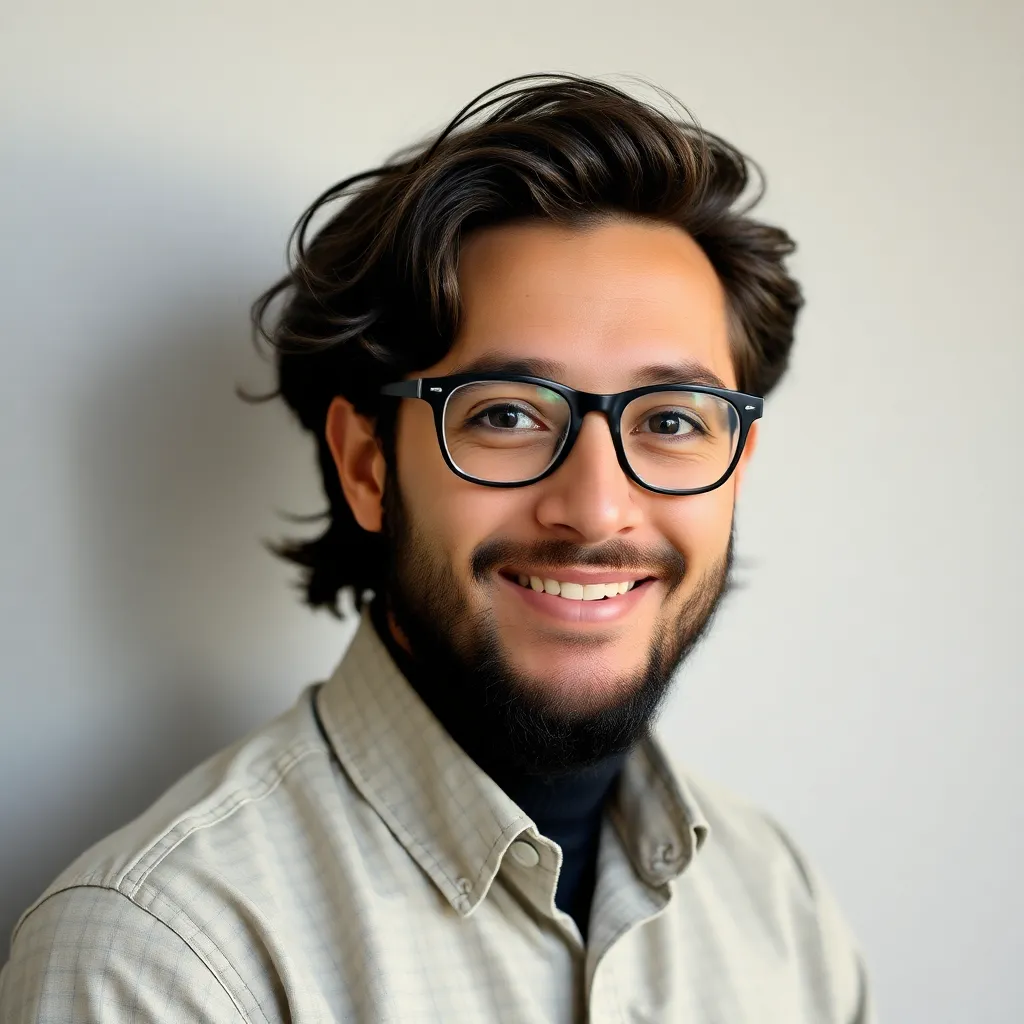
adminse
Apr 19, 2025 · 8 min read

Table of Contents
What is MRP in Supply Chain? Unveiling the Power of Materials Requirements Planning
What if optimizing your entire supply chain hinged on a single, powerful planning system? Materials Requirements Planning (MRP) is that system, a cornerstone of efficient and responsive supply chain management.
Editor’s Note: This article on Materials Requirements Planning (MRP) in supply chain management was published today, providing readers with the latest insights and understanding of this crucial planning tool.
Why MRP Matters: Streamlining Production and Inventory
Materials Requirements Planning (MRP) is a production planning and inventory control system used to determine the materials and components needed to manufacture a product. It goes beyond simple inventory tracking; MRP is a sophisticated system that integrates production scheduling, inventory management, and purchasing to ensure that the right materials are available at the right time in the right quantities. Its importance lies in its ability to minimize inventory holding costs, reduce production delays caused by material shortages, and improve overall supply chain efficiency. In today's dynamic business environment, MRP helps companies respond rapidly to changing market demands and customer orders, securing a competitive advantage. Its applications are far-reaching, spanning diverse industries from manufacturing and automotive to electronics and pharmaceuticals.
Overview: What This Article Covers
This article delves into the core aspects of MRP in supply chain management, exploring its definition, functionality, key inputs, outputs, different types, advantages, limitations, and its integration with other supply chain technologies. Readers will gain actionable insights and a comprehensive understanding of how MRP contributes to streamlined production and improved profitability.
The Research and Effort Behind the Insights
This article is the result of extensive research, drawing upon reputable academic journals, industry reports, and case studies from leading companies utilizing MRP systems. The information presented is supported by data-driven evidence and expert opinions, ensuring accuracy and reliability for readers. A structured approach has been employed to ensure clarity and easy comprehension.
Key Takeaways:
- Definition and Core Concepts: A precise understanding of MRP and its fundamental principles.
- Inputs and Outputs: Identifying the crucial data required and the valuable information generated by MRP systems.
- Different Types of MRP: Exploring variations like Closed-Loop MRP and Manufacturing Resource Planning (MRP II).
- Advantages and Limitations: Weighing the benefits against the potential drawbacks.
- Implementation and Integration: Strategies for successful MRP implementation and integration with other systems.
- Future Trends: Examining the evolution of MRP and its adaptation to emerging technologies.
Smooth Transition to the Core Discussion:
Having established the importance of MRP, let's now explore its key components and functionalities in detail. Understanding these elements will unlock the true potential of MRP within a modern supply chain.
Exploring the Key Aspects of MRP
1. Definition and Core Concepts:
MRP is a computer-based inventory management system that uses a bill of materials (BOM), an inventory master file, and a master production schedule (MPS) to calculate the exact quantities of materials required to produce a product over a given time horizon. It works by "exploding" the BOM – a hierarchical listing of all raw materials, sub-assemblies, intermediate assemblies, sub-components, parts, and the quantities of each needed to manufacture an end product – to determine the net requirements for each item at each level. The system then schedules the procurement or production of these materials to meet the demands dictated by the MPS. The goal is to ensure that materials are available when needed, minimizing both inventory carrying costs and the risk of production delays due to material shortages.
2. Inputs to an MRP System:
Several crucial inputs feed into an MRP system to generate accurate plans. These include:
- Master Production Schedule (MPS): This is a high-level plan specifying the quantity of each finished product that the company plans to manufacture over a specific period. It's the driving force behind MRP calculations.
- Bill of Materials (BOM): As mentioned previously, this is a comprehensive list of all the raw materials, components, and sub-assemblies needed to produce a finished product. The accuracy of the BOM is paramount for accurate MRP calculations.
- Inventory Records: This file keeps track of current inventory levels for all items, including raw materials, work-in-progress (WIP), and finished goods. It provides real-time visibility into available inventory.
- Lead Times: These are the times required to procure or manufacture each item. Accurate lead time data is essential for proper scheduling.
3. Outputs of an MRP System:
The MRP system generates several key outputs that guide production and purchasing activities:
- Planned Order Releases: This indicates the quantities and timing of planned orders for materials or components.
- Rescheduling Reports: These highlight potential delays or shortages and suggest adjustments to the MPS or production schedules.
- Exception Reports: These draw attention to critical issues, such as low inventory levels or potential delays that require immediate action.
- Purchase Orders: Based on planned order releases, the system generates purchase orders for required materials.
- Work Orders: These direct the production team to manufacture specific components or sub-assemblies.
4. Different Types of MRP:
- Basic MRP (Closed-Loop MRP): This is the fundamental MRP system, focusing on material requirements planning based on the MPS and BOM. It primarily addresses material needs and scheduling.
- Manufacturing Resource Planning (MRP II): This is an evolution of basic MRP, expanding its scope to encompass capacity planning, financial planning, and other aspects of the manufacturing process. It integrates production planning, inventory control, capacity management, and financial management into a single, cohesive system.
5. Advantages of Using MRP:
- Improved Inventory Control: Reduces excess inventory and minimizes stockouts.
- Enhanced Production Scheduling: Optimizes production processes and minimizes delays.
- Reduced Production Costs: Minimizes waste and improves efficiency.
- Better Customer Service: Ensures timely delivery of finished products.
- Improved Forecasting Accuracy: Uses data-driven insights for more accurate demand forecasts.
6. Limitations of MRP:
- Data Dependency: The accuracy of MRP heavily relies on the accuracy of input data (BOM, inventory levels, lead times, etc.). Inaccurate data will lead to inaccurate plans.
- Complexity: Implementing and managing an MRP system can be complex and require specialized expertise.
- Cost: Implementing and maintaining an MRP system can involve significant costs.
- Static Nature: Traditional MRP systems may struggle to adapt to rapidly changing demands.
- Limited Scope: Basic MRP primarily focuses on materials; it doesn't directly manage all resources (human, machinery).
7. Implementation and Integration:
Successful MRP implementation requires careful planning and execution. Key steps include:
- Data Cleansing and Validation: Ensuring the accuracy and consistency of input data.
- System Selection: Choosing an appropriate MRP software system that fits the company's needs.
- Training and Education: Providing adequate training to personnel involved in using the system.
- Integration with Other Systems: Integrating MRP with ERP (Enterprise Resource Planning) and other relevant systems for seamless data flow.
Closing Insights: Summarizing the Core Discussion
MRP is a powerful tool for optimizing supply chain efficiency. By accurately planning material requirements, it minimizes waste, reduces lead times, and improves overall production effectiveness. However, successful implementation hinges on accurate data, proper system selection, and robust integration with other business systems.
Exploring the Connection Between Demand Forecasting and MRP
The relationship between demand forecasting and MRP is crucial. Accurate demand forecasting forms the foundation of the Master Production Schedule (MPS), which, in turn, drives the MRP system. Inaccurate demand forecasts lead to inaccurate MPS, resulting in flawed material requirements planning and potential stockouts or excess inventory.
Key Factors to Consider:
- Roles and Real-World Examples: Accurate demand forecasting, whether based on historical data, market trends, or sales projections, directly influences the MPS. A company producing seasonal products would require a highly accurate seasonal demand forecast to generate an effective MPS and subsequently an effective MRP plan.
- Risks and Mitigations: Poor forecasting methods can lead to significant inventory discrepancies. Mitigation involves using robust forecasting techniques, regularly reviewing forecasts, and incorporating real-time sales data.
- Impact and Implications: The impact of inaccurate forecasting ripples through the entire supply chain, affecting production scheduling, purchasing decisions, and ultimately, profitability.
Conclusion: Reinforcing the Connection
The interplay between demand forecasting and MRP underscores the importance of accurate data in supply chain management. Investing in robust forecasting techniques and integrating them seamlessly with the MRP system is crucial for achieving optimal supply chain performance.
Further Analysis: Examining Demand Forecasting in Greater Detail
Several methods exist for demand forecasting, each with its strengths and weaknesses. These include time series analysis, causal modeling, and market research. The choice of method depends on factors such as data availability, forecasting horizon, and the nature of the product.
FAQ Section: Answering Common Questions About MRP
- What is the difference between MRP and ERP? MRP is a component of ERP. ERP is a broader system integrating all aspects of a business, while MRP specifically focuses on production planning and inventory control.
- Can MRP be used in service industries? While traditionally associated with manufacturing, adapted versions of MRP principles can be applied to service industries to optimize resource allocation and scheduling.
- How can I choose the right MRP software? Consider factors like your company's size, industry, specific needs, budget, and the software's features and scalability.
Practical Tips: Maximizing the Benefits of MRP
- Data Integrity: Prioritize data accuracy and consistency by implementing robust data validation procedures.
- Regular Reviews: Regularly review and adjust the MPS and MRP plans to adapt to changes in demand or unforeseen circumstances.
- Collaboration: Foster collaboration between different departments (production, purchasing, sales) to ensure seamless data flow and efficient communication.
Final Conclusion: Wrapping Up with Lasting Insights
MRP remains a cornerstone of efficient supply chain management. While technology continues to evolve, the fundamental principles of planning material requirements remain crucial for optimizing production, controlling inventory, and ensuring timely delivery of goods. By understanding and effectively utilizing MRP, businesses can gain a significant competitive advantage in today's dynamic market.
Latest Posts
Related Post
Thank you for visiting our website which covers about What Is Mrp In Supply Chain . We hope the information provided has been useful to you. Feel free to contact us if you have any questions or need further assistance. See you next time and don't miss to bookmark.