What Are Different Types Of Costing
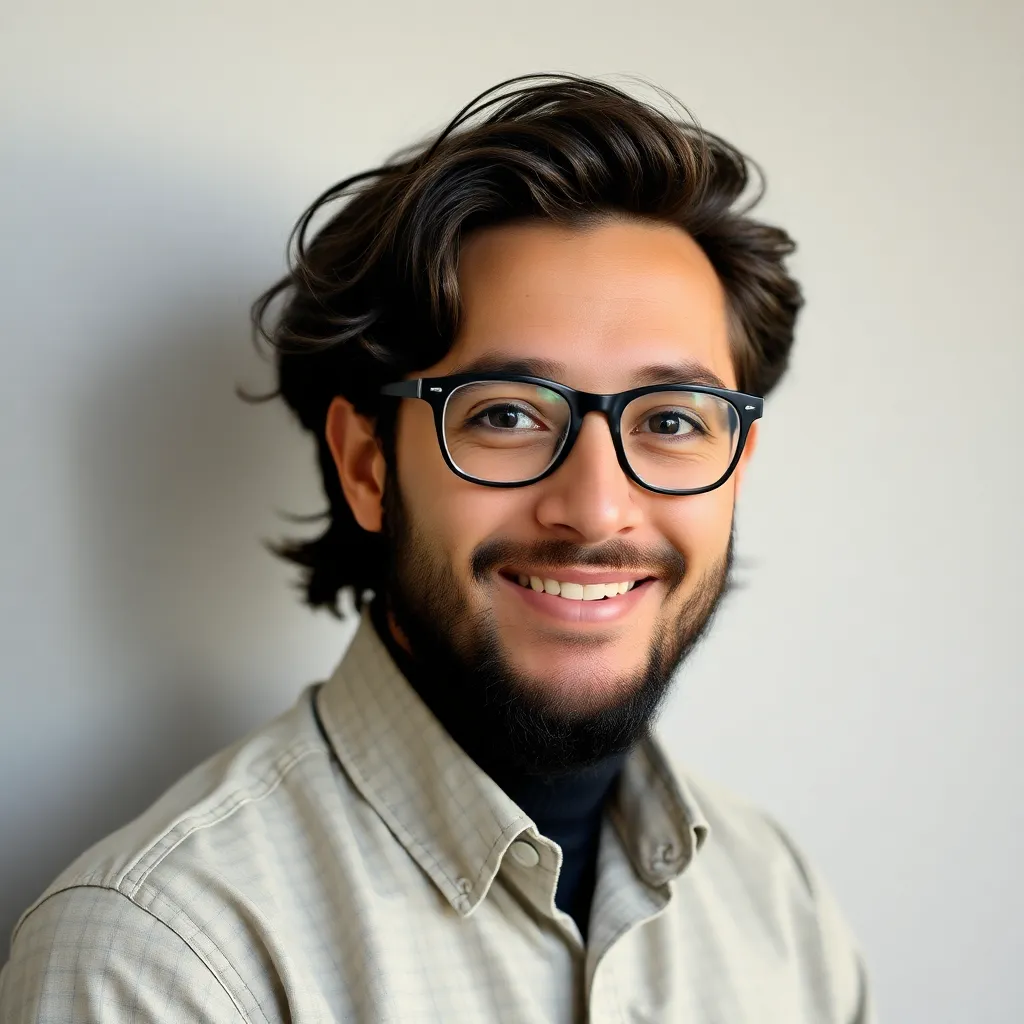
adminse
Mar 28, 2025 · 9 min read

Table of Contents
Decoding the Diverse World of Costing Methods: A Comprehensive Guide
What if the future of successful business hinges on accurately understanding and applying the right costing method? Mastering costing is not just about numbers; it's about strategic decision-making that drives profitability and sustainable growth.
Editor’s Note: This article on different types of costing methods provides a comprehensive overview of the various approaches used in business accounting. It's designed to equip readers with a solid understanding of these methods and their applications, enabling them to make informed financial decisions. This information is current and relevant for businesses of all sizes.
Why Understanding Different Costing Methods Matters:
In today's competitive business landscape, accurate cost accounting is paramount. Understanding your costs – both direct and indirect – is fundamental to pricing strategies, profitability analysis, inventory management, and overall business planning. Different costing methods offer varied perspectives on cost allocation, each suited to specific business contexts and objectives. From small startups to multinational corporations, the ability to effectively analyze and manage costs directly impacts the bottom line and long-term sustainability.
Overview: What This Article Covers:
This in-depth article will explore the key costing methods employed in various industries. We will examine their core principles, applications, advantages, and limitations. We'll cover traditional methods like absorption costing and variable costing, alongside more advanced techniques such as activity-based costing and target costing. The article will also analyze the situations where each method is most appropriate, empowering you to select the best approach for your specific business needs.
The Research and Effort Behind the Insights:
This analysis is the result of extensive research drawing from reputable accounting textbooks, professional journals, and real-world case studies. We've synthesized this information to provide a clear, practical, and accessible guide to costing methods for businesses of all sizes and complexities.
Key Takeaways:
- Definition and Core Concepts: A clear definition of costing and its foundational principles.
- Traditional Methods: A detailed exploration of absorption costing and variable costing, including their strengths and weaknesses.
- Advanced Methods: An in-depth look at activity-based costing and target costing, highlighting their applications and benefits.
- Choosing the Right Method: A practical guide on selecting the most suitable costing method based on specific business needs.
- Real-world Examples: Illustrative examples to demonstrate the practical application of each method.
Smooth Transition to the Core Discussion:
Now that we've established the importance of understanding different costing methods, let's delve into a detailed examination of the various approaches available. We'll begin with a review of the more traditional methods before exploring the more sophisticated techniques used in today's business environment.
Exploring the Key Aspects of Different Costing Methods:
1. Traditional Costing Methods:
-
Absorption Costing (Full Costing): This is a traditional method that allocates all manufacturing costs (direct materials, direct labor, and both variable and fixed manufacturing overhead) to the cost of goods sold. Fixed manufacturing overhead is absorbed into the product cost based on a predetermined overhead rate (often based on machine hours or direct labor hours).
- Advantages: Provides a complete product cost, useful for pricing decisions and inventory valuation. Complies with generally accepted accounting principles (GAAP) for external reporting.
- Disadvantages: Can distort profitability analysis, as fixed costs are allocated to products regardless of production volume. It can lead to inaccurate cost information when production levels fluctuate significantly.
-
Variable Costing (Direct Costing): This method only includes variable manufacturing costs (direct materials, direct labor, and variable manufacturing overhead) in the cost of goods sold. Fixed manufacturing overhead is treated as a period cost and expensed in the period incurred.
- Advantages: Provides a clearer picture of the impact of production volume on profitability. It simplifies cost-volume-profit (CVP) analysis. Facilitates better short-term decision-making.
- Disadvantages: Doesn't meet GAAP requirements for external financial reporting. Doesn't provide a complete product cost, which can be a limitation for certain pricing strategies.
2. Advanced Costing Methods:
-
Activity-Based Costing (ABC): This method assigns costs to activities and then allocates those costs to products based on their consumption of those activities. This provides a more accurate cost allocation than traditional methods, particularly in complex manufacturing environments with multiple products and processes.
- Advantages: Provides a more accurate picture of product costs, especially when overhead costs are significant. Identifies cost drivers and helps in cost reduction efforts. Useful for strategic decision-making related to product lines and process improvements.
- Disadvantages: More complex and time-consuming than traditional methods. Requires detailed data collection and analysis. Can be costly to implement.
-
Target Costing: This is a proactive approach where the target cost of a product is determined based on the desired selling price and profit margin. Companies then engineer and design the product to meet the target cost.
- Advantages: Focuses on cost reduction from the design stage. Improves profitability by ensuring that costs align with market prices. Encourages innovation and efficiency in product development.
- Disadvantages: Requires accurate market research and demand forecasting. Can be challenging to achieve target costs, especially for complex products. Might compromise product quality if cost reduction is overly aggressive.
3. Other Costing Methods:
Beyond these core methods, various other costing techniques exist, tailored to specific industries and situations:
- Lean Accounting: Integrates lean manufacturing principles with cost accounting, focusing on eliminating waste and improving efficiency.
- Throughput Accounting: Measures profitability based on throughput (revenue generated from sales), emphasizing the importance of operational efficiency.
- Life Cycle Costing: Considers all costs associated with a product throughout its entire life cycle, from design and development to disposal.
- Job Order Costing: Tracks costs for individual projects or jobs, often used in custom manufacturing or service industries.
- Process Costing: Assigns costs to homogeneous units of production, suitable for mass production environments.
Exploring the Connection Between Overhead Allocation and Cost Accuracy:
Overhead allocation significantly impacts the accuracy of costing methods. Traditional methods often use simplistic allocation bases (like direct labor hours or machine hours), potentially leading to inaccurate cost assignments, especially when diverse products consume overhead resources differently. ABC costing addresses this limitation by identifying and allocating costs based on specific activities and their associated drivers, resulting in more precise cost information.
Key Factors to Consider:
-
Roles and Real-World Examples: Many companies successfully employ ABC costing to identify and eliminate cost inefficiencies. For instance, a manufacturing company might use ABC to discover that a particular product line consumes a disproportionate amount of setup time, leading to higher costs than previously recognized.
-
Risks and Mitigations: The major risk with ABC is the cost and complexity of implementation. Companies can mitigate this by focusing on the most significant cost drivers and gradually expanding the system over time.
-
Impact and Implications: Accurate cost information enables more effective pricing, better resource allocation, and more informed strategic decisions. Inaccurate costing can lead to underpricing, reduced profitability, and ultimately, business failure.
Conclusion: Reinforcing the Connection:
The connection between overhead allocation and cost accuracy is undeniable. Using appropriate costing methods, especially advanced techniques like ABC, significantly improves the accuracy of cost information. This accuracy, in turn, allows for better decision-making in pricing, production planning, and resource allocation, leading to enhanced profitability and business sustainability.
Further Analysis: Examining Activity-Based Costing in Greater Detail:
Activity-Based Costing (ABC) is a powerful tool that can significantly improve the accuracy of cost allocation. It involves identifying the activities that consume resources, assigning costs to these activities, and then allocating these costs to products based on their consumption of activities. This differs significantly from traditional methods that often rely on simplistic allocation bases like direct labor hours or machine hours.
ABC utilizes cost pools and cost drivers. A cost pool is a group of similar costs associated with a specific activity. A cost driver is a factor that causes the cost pool's costs to change. For instance, machine setups could be a cost pool, and the number of setups could be the cost driver. By accurately identifying these cost drivers and their relationships to products, ABC allows for a more precise allocation of overhead costs. The result is a clearer and more accurate understanding of the true cost of each product.
FAQ Section: Answering Common Questions About Costing Methods:
-
Q: What is the best costing method to use? A: There's no single "best" method. The optimal choice depends on factors like the complexity of the manufacturing process, the number of products, the level of detail required, and the company's specific needs.
-
Q: How does absorption costing differ from variable costing? A: Absorption costing includes all manufacturing costs (fixed and variable) in the product cost, while variable costing only includes variable manufacturing costs.
-
Q: What are the limitations of traditional costing methods? A: Traditional methods often use simplistic allocation bases that may not accurately reflect the consumption of overhead resources by different products.
-
Q: What are the benefits of Activity-Based Costing (ABC)? A: ABC provides more accurate cost information by assigning costs based on activities and their cost drivers. This leads to improved decision-making and better cost control.
-
Q: Is target costing suitable for all industries? A: While target costing can benefit many industries, it is particularly effective in industries with high competition and price sensitivity.
Practical Tips: Maximizing the Benefits of Different Costing Methods:
- Understand your business: Before choosing a costing method, carefully analyze your production processes, cost structure, and business objectives.
- Collect accurate data: Accurate data is essential for any costing method. Ensure that your data collection systems are reliable and efficient.
- Choose the right method: Select a costing method that aligns with your business needs and level of complexity.
- Regularly review and refine: Costing methods should be regularly reviewed and adjusted to reflect changes in your business environment.
- Use costing information for strategic decision-making: Don’t let costing data sit unused. Use it to improve pricing, production planning, and resource allocation.
Final Conclusion: Wrapping Up with Lasting Insights:
Understanding and effectively applying the appropriate costing method is crucial for the financial health and success of any business. While traditional methods have their place, advanced techniques like ABC provide a more accurate and comprehensive understanding of product costs, enabling businesses to make informed strategic decisions. By mastering the nuances of different costing methods, businesses can optimize pricing, improve resource allocation, enhance profitability, and gain a crucial competitive edge. The right costing approach empowers companies to navigate the complexities of the modern business landscape and achieve sustainable growth.
Latest Posts
Latest Posts
-
Independent Auditor Definition Rules Importance
Apr 24, 2025
-
Indentured Servitude Definition History And Controversy
Apr 24, 2025
-
Independent 401k Definition
Apr 24, 2025
-
Indemnification Method Definition
Apr 24, 2025
-
Indenture Definition And Types In Finance
Apr 24, 2025
Related Post
Thank you for visiting our website which covers about What Are Different Types Of Costing . We hope the information provided has been useful to you. Feel free to contact us if you have any questions or need further assistance. See you next time and don't miss to bookmark.