Working Control Definition
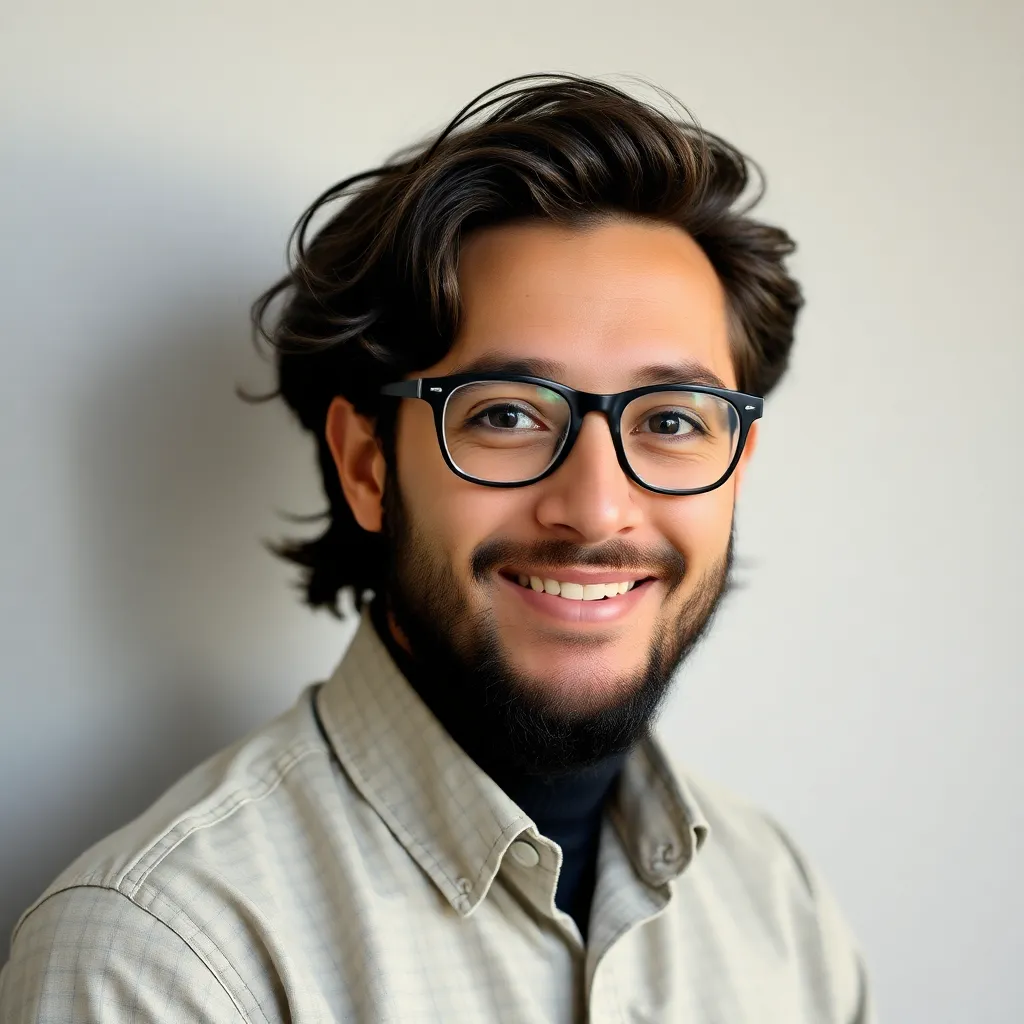
adminse
Mar 21, 2025 · 9 min read

Table of Contents
Unveiling the Power of Working Control: A Deep Dive into Definition, Applications, and Implications
What if the future of efficient operations hinges on a deep understanding of working control? This crucial concept, often overlooked, is the backbone of productivity, innovation, and sustainable growth across diverse industries.
Editor’s Note: This comprehensive article on working control provides a detailed exploration of its definition, applications, and implications. Updated with the latest insights, this resource aims to equip readers with a robust understanding of this pivotal management concept.
Why Working Control Matters: Relevance, Practical Applications, and Industry Significance
Working control, in its essence, refers to the systematic process of monitoring, measuring, and regulating activities to ensure they align with predetermined plans and objectives. It's not merely about checking if tasks are completed; it's about proactively identifying deviations, analyzing their root causes, and implementing corrective actions to maintain optimal performance. Its relevance spans numerous sectors, from manufacturing and logistics to healthcare and finance. In manufacturing, effective working control minimizes waste, streamlines processes, and ensures product quality. In healthcare, it improves patient safety and enhances operational efficiency. In finance, it reduces risks, improves compliance, and optimizes resource allocation. The impact of robust working control is undeniable: increased productivity, reduced costs, improved quality, and enhanced overall competitiveness.
Overview: What This Article Covers
This article delves into the core aspects of working control, exploring its various definitions, practical applications across industries, associated challenges, and its future implications. Readers will gain a comprehensive understanding of this critical management concept, supported by real-world examples and insightful analysis. We will examine the relationship between working control and other key management principles, and explore how different organizational structures influence its implementation.
The Research and Effort Behind the Insights
This article is the result of extensive research, drawing upon established management literature, industry best practices, and case studies from diverse sectors. The analysis incorporates insights from leading management thinkers, operational experts, and quantitative data to ensure accuracy and relevance. The information presented is meticulously reviewed to offer a reliable and up-to-date perspective on working control.
Key Takeaways:
- Definition and Core Concepts: A precise definition of working control, exploring its fundamental principles and components.
- Practical Applications: Diverse examples of working control implementation across various industries and organizational structures.
- Challenges and Solutions: Identification of common obstacles in implementing working control and strategies for overcoming them.
- Future Implications: The evolving role of working control in the context of technological advancements and changing business landscapes.
- The Interplay of Working Control and Other Management Principles: Exploring the synergistic relationship between working control and other essential management elements.
Smooth Transition to the Core Discussion:
Having established the significance of working control, let's now embark on a detailed exploration of its key aspects, unraveling its complexities and unveiling its transformative potential.
Exploring the Key Aspects of Working Control
1. Definition and Core Concepts:
Working control encompasses a multifaceted approach to managing operations. At its core, it involves the following key elements:
- Planning: Establishing clear objectives, setting targets, and defining the required processes and resources.
- Monitoring: Continuously tracking progress against established plans, using appropriate metrics and data collection methods.
- Measuring: Quantifying performance against pre-defined benchmarks, identifying deviations from planned targets.
- Controlling: Taking corrective actions to address deviations, ensuring performance aligns with objectives.
- Feedback Loop: Utilizing data and insights from the monitoring and measuring phases to refine future plans and strategies.
Effective working control requires a combination of quantitative and qualitative measures. Quantitative measures, such as production output, defect rates, and customer satisfaction scores, provide objective data. Qualitative measures, such as employee morale, process efficiency, and team collaboration, provide valuable contextual insights. A balanced approach ensures a comprehensive understanding of performance.
2. Applications Across Industries:
Working control finds widespread application across a variety of industries. Here are some examples:
- Manufacturing: Working control is crucial for maintaining consistent product quality, optimizing production processes, and minimizing waste. Statistical Process Control (SPC) and Six Sigma methodologies are often employed for precise control.
- Logistics and Supply Chain: Working control ensures timely delivery of goods, efficient inventory management, and optimal resource allocation. Real-time tracking systems and inventory management software are integral components.
- Healthcare: In hospitals and clinics, working control is essential for ensuring patient safety, optimizing resource utilization, and improving operational efficiency. Key performance indicators (KPIs) such as patient wait times, infection rates, and medication errors are closely monitored.
- Finance: Financial institutions utilize working control for risk management, regulatory compliance, and accurate financial reporting. Internal controls and audit trails are crucial components.
- Project Management: Working control is essential for ensuring projects are completed on time, within budget, and to the required specifications. Project management software and Gantt charts facilitate progress tracking and control.
3. Challenges and Solutions:
Implementing effective working control is not without its challenges:
- Resistance to Change: Employees may resist changes to established processes, hindering the effectiveness of control measures. Overcoming this requires clear communication, training, and effective change management strategies.
- Data Overload: Excessive data can overwhelm decision-makers, hindering the ability to identify and address critical issues. Effective data visualization and analysis tools can mitigate this challenge.
- Lack of Resources: Insufficient resources, such as personnel, technology, or budget, can limit the effectiveness of control measures. Strategic resource allocation and prioritization are crucial.
- Inadequate Training: Lack of training for employees on the use of control systems and procedures can lead to errors and inefficiencies. Regular training and development programs are necessary.
Addressing these challenges requires a proactive approach, including thorough planning, stakeholder engagement, appropriate technology implementation, and continuous improvement efforts.
4. Impact on Innovation:
Contrary to some misconceptions, working control does not stifle innovation. In fact, it can actively foster innovation by providing a framework for testing new ideas and processes. By closely monitoring the results of experiments and implementing corrective actions, organizations can refine their approach and accelerate the innovation process.
Closing Insights: Summarizing the Core Discussion
Working control is not simply a set of procedures; it's a dynamic management philosophy that facilitates continuous improvement and sustainable growth. Its successful implementation requires a commitment to data-driven decision-making, proactive problem-solving, and a culture of continuous learning. Organizations that effectively integrate working control into their operations are better positioned to achieve their objectives, enhance efficiency, and adapt to changing market conditions.
Exploring the Connection Between Feedback Mechanisms and Working Control
Feedback mechanisms are integral to effective working control. They provide the essential data and insights needed to monitor performance, identify deviations, and implement corrective actions. Without robust feedback mechanisms, working control becomes reactive rather than proactive, limiting its effectiveness.
Key Factors to Consider:
- Roles and Real-World Examples: Effective feedback mechanisms often involve multiple stakeholders, from frontline employees to senior management. For example, in a manufacturing setting, feedback might come from quality control inspectors, production line workers, and customer service representatives. This data is then analyzed by management to identify trends and implement corrective actions.
- Risks and Mitigations: Delayed or inaccurate feedback can lead to significant problems. To mitigate this risk, organizations should implement systems for timely data collection, analysis, and dissemination. Regular audits and reviews of feedback mechanisms are also essential.
- Impact and Implications: The quality and timeliness of feedback directly impact the effectiveness of working control. Prompt and accurate feedback enables proactive adjustments, minimizing disruptions and maximizing efficiency. Conversely, delayed or inaccurate feedback can lead to significant losses and damage to reputation.
Conclusion: Reinforcing the Connection
The synergy between feedback mechanisms and working control is undeniable. Effective feedback mechanisms are the lifeblood of working control, enabling proactive adjustments, continuous improvement, and sustainable growth. Organizations that prioritize robust feedback systems are better equipped to navigate challenges, optimize performance, and thrive in dynamic environments.
Further Analysis: Examining Feedback Mechanisms in Greater Detail
Feedback mechanisms can be categorized into several types, including:
- Real-time feedback: This involves immediate feedback during the operational process, enabling instant adjustments. Examples include automated quality control systems in manufacturing and real-time tracking systems in logistics.
- Periodic feedback: This involves regular, scheduled feedback, such as monthly performance reviews or quarterly reports.
- Customer feedback: This involves gathering feedback from customers through surveys, reviews, or other channels.
- Employee feedback: This involves soliciting feedback from employees through surveys, suggestion boxes, or regular meetings.
The choice of feedback mechanisms depends on the specific context, the nature of the operations, and the information needed for effective control. A combination of different mechanisms is often most effective.
FAQ Section: Answering Common Questions About Working Control
-
Q: What is the difference between working control and quality control?
-
A: While both are crucial for operational excellence, working control is a broader concept encompassing all aspects of managing operations to achieve objectives, while quality control focuses specifically on ensuring that products or services meet predefined quality standards.
-
Q: How can small businesses implement effective working control?
-
A: Even small businesses can benefit from working control by using simple, yet effective tools such as checklists, regular meetings, and performance tracking spreadsheets. Focus should be placed on key performance indicators relevant to the business.
-
Q: What are the key metrics for measuring the effectiveness of working control?
-
A: Key metrics vary depending on the context, but some common ones include production efficiency, defect rates, customer satisfaction, on-time delivery, and employee morale.
-
Q: How can technology enhance working control?
-
A: Technology plays a critical role by automating data collection, providing real-time insights, and enabling more precise control measures. Examples include Enterprise Resource Planning (ERP) systems, Business Intelligence (BI) tools, and process automation software.
Practical Tips: Maximizing the Benefits of Working Control
- Clearly Define Objectives: Begin by setting clear, measurable, achievable, relevant, and time-bound (SMART) objectives.
- Develop Robust Metrics: Identify key performance indicators (KPIs) that accurately reflect progress towards objectives.
- Implement Effective Monitoring Systems: Establish processes for regularly monitoring performance against KPIs.
- Establish Clear Communication Channels: Ensure efficient communication of performance data and corrective actions.
- Foster a Culture of Continuous Improvement: Encourage feedback, learning, and ongoing adjustments to processes.
Final Conclusion: Wrapping Up with Lasting Insights
Working control represents a cornerstone of efficient and effective operations. By understanding its principles, implementing robust systems, and fostering a culture of continuous improvement, organizations can unlock significant gains in productivity, quality, and overall performance. The insights presented in this article provide a comprehensive framework for implementing effective working control and achieving lasting operational excellence.
Latest Posts
Related Post
Thank you for visiting our website which covers about Working Control Definition . We hope the information provided has been useful to you. Feel free to contact us if you have any questions or need further assistance. See you next time and don't miss to bookmark.