What To Do When Taking Inventory In A Small Business
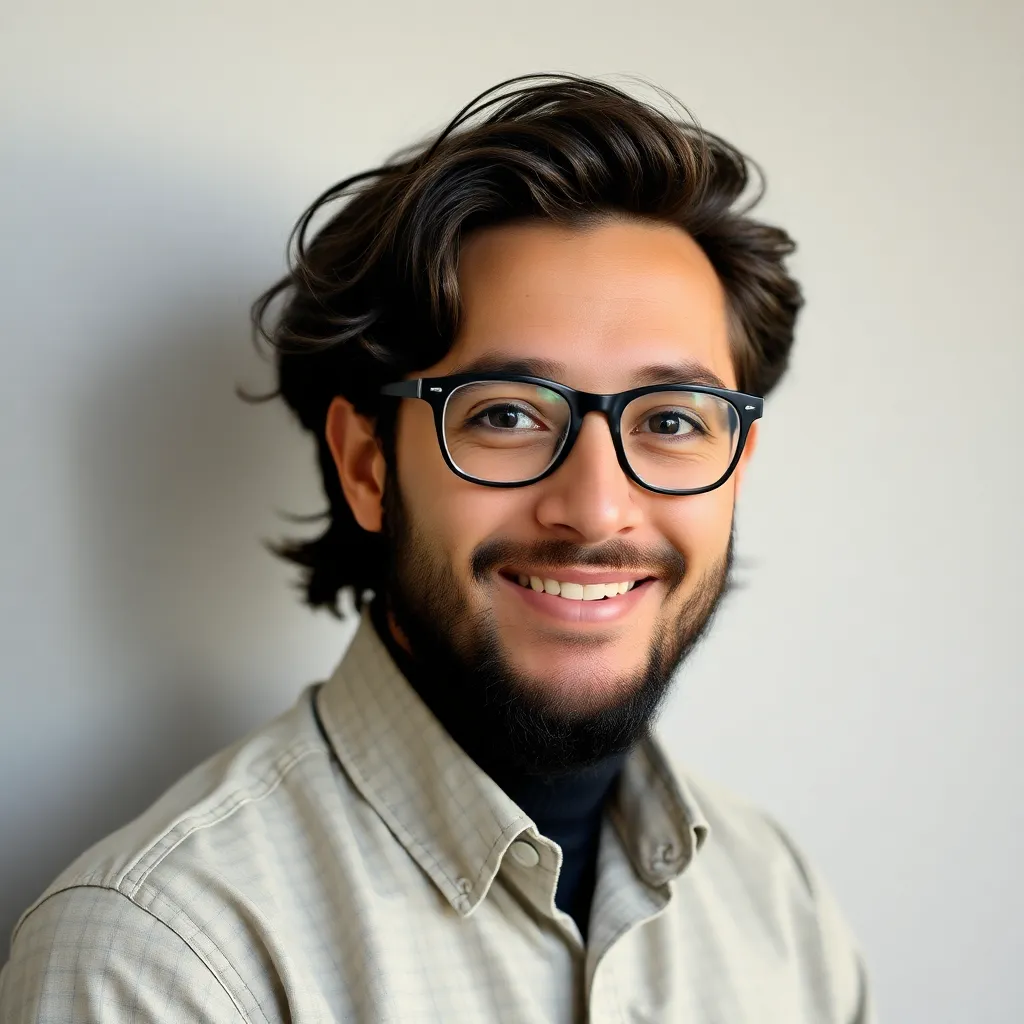
adminse
Apr 13, 2025 · 8 min read

Table of Contents
Conquer Inventory Chaos: A Small Business Guide to Accurate and Efficient Stocktaking
What if inaccurate inventory crippled your small business's growth potential? Mastering inventory management is crucial for profitability and success.
Editor’s Note: This comprehensive guide to small business inventory taking was updated today to reflect current best practices and software solutions. We've included practical tips and strategies to help you streamline your process and minimize disruptions.
Why Accurate Inventory Matters:
Accurate inventory is the bedrock of a healthy small business. It impacts everything from cash flow and profitability to customer satisfaction and future planning. Overstocking ties up capital, leading to storage costs and potential spoilage. Understocking results in lost sales, unhappy customers, and damaged reputation. Understanding your inventory levels allows for informed purchasing decisions, optimized pricing strategies, and improved forecasting. Data-driven insights derived from accurate stocktaking allow you to identify slow-moving items, predict demand fluctuations, and proactively manage your supply chain. This ultimately translates into increased efficiency, reduced waste, and greater profitability.
Overview: What This Article Covers:
This article provides a step-by-step guide to efficient and accurate inventory taking for small businesses. We'll cover planning your inventory count, choosing the right method, utilizing technology, managing discrepancies, and implementing ongoing inventory control strategies. You'll gain actionable insights and practical tips to streamline your process and minimize disruptions to your daily operations.
The Research and Effort Behind the Insights:
This guide draws upon years of experience in small business consulting, combined with research into inventory management best practices and current software solutions. We have consulted numerous case studies and incorporated feedback from small business owners across various industries to provide practical, real-world advice. The strategies outlined are designed to be adaptable to different business models and scales.
Key Takeaways:
- Planning & Preparation: The importance of meticulous planning before commencing the inventory count.
- Inventory Counting Methods: A comparison of cycle counting, periodic counting, and perpetual inventory systems.
- Technology Integration: The role of barcode scanners, inventory management software, and mobile devices in streamlining the process.
- Reconciling Discrepancies: Strategies for identifying and addressing inventory discrepancies.
- Post-Inventory Actions: Utilizing inventory data for informed business decisions.
Smooth Transition to the Core Discussion:
Now that we've established the critical role of accurate inventory, let's dive into the practical steps involved in conducting a successful inventory count for your small business.
Exploring the Key Aspects of Inventory Taking:
1. Planning and Preparation:
Before you even begin counting, thorough planning is essential. This stage sets the foundation for a smooth and accurate inventory count.
- Define Scope: Clearly identify which items will be included in the inventory count. This might include raw materials, work-in-progress, finished goods, and supplies.
- Schedule Downtime: Determine a time when your business can be minimally disrupted. Weekends or slow periods are ideal. Communicate the schedule clearly to your team.
- Gather Supplies: Assemble necessary materials such as barcode scanners (if applicable), inventory count sheets, pens, calculators, and possibly a mobile device for data entry.
- Team Allocation: If your inventory is extensive, divide the task amongst your team, assigning specific areas or product categories to each person. Ensure clear communication channels and a designated leader.
- Training: If using new technology or methods, provide adequate training to your team beforehand.
- Inventory Forms Design: Create clear and concise inventory count sheets. These sheets should include columns for item number, description, quantity on hand, unit cost, and location.
2. Choosing the Right Inventory Counting Method:
Several methods exist for taking inventory. The best choice depends on your business size, inventory complexity, and resources.
- Periodic Inventory System: This traditional method involves a complete physical count of all inventory at fixed intervals (e.g., quarterly, annually). It's simple for smaller businesses with low inventory turnover but can be time-consuming and disruptive.
- Cycle Counting: This method involves counting a small portion of your inventory regularly, rather than a full count. This reduces disruption and provides a more continuous understanding of inventory levels. It's suitable for businesses with larger and more complex inventories.
- Perpetual Inventory System: This system uses technology (POS systems, barcode scanners, inventory management software) to track inventory levels in real-time. This offers the most accurate and up-to-date inventory information but requires a significant investment in technology.
3. Utilizing Technology:
Technology significantly streamlines the inventory process.
- Barcode Scanners: These devices quickly scan barcodes, automatically recording item numbers and quantities. This dramatically reduces errors and speeds up the process.
- Inventory Management Software: Software solutions automate various aspects of inventory management, including tracking, forecasting, and reporting. Many offer mobile apps for on-the-go data entry.
- Mobile Devices: Tablets and smartphones can be used for data entry directly into inventory management software, eliminating manual data transcription.
- Cloud-Based Solutions: Cloud-based inventory systems offer accessibility from anywhere with an internet connection, facilitating collaboration and real-time data updates.
4. Managing Discrepancies:
Discrepancies between counted inventory and recorded inventory are inevitable. The key is to identify and address them efficiently.
- Double-Checking: Implement a system of double-checking counts to minimize errors. Assigning two people to count the same items is a useful strategy.
- Investigating Discrepancies: When discrepancies are identified, thoroughly investigate their cause. This might involve checking for damaged or misplaced items, reviewing purchase orders, or inspecting sales records.
- Documentation: Meticulously document all discrepancies, including their cause and resolution. This information is valuable for improving future inventory processes.
- Adjusting Inventory: Make necessary adjustments to your inventory records to reflect the actual count. This ensures your inventory data is accurate and reliable.
5. Post-Inventory Actions:
Once the inventory count is complete, several critical steps remain.
- Data Analysis: Analyze the inventory data to identify slow-moving items, potential overstocking, or areas where demand is unexpectedly high.
- Reporting: Generate reports summarizing inventory levels, values, and any identified discrepancies. Share these reports with relevant stakeholders.
- Actionable Insights: Use the data to make informed decisions about purchasing, pricing, and future inventory planning.
- Process Improvements: Evaluate your inventory process to identify areas for improvement. This might involve streamlining procedures, implementing new technology, or adjusting team roles.
Exploring the Connection Between Technology and Efficient Inventory:
The relationship between technology and efficient inventory is symbiotic. Technology acts as a catalyst for accuracy and efficiency, minimizing human error and optimizing processes.
Key Factors to Consider:
- Roles and Real-World Examples: Businesses utilizing barcode scanners and inventory management software experience significantly faster and more accurate counts compared to manual methods. A small retail store using a POS system integrated with inventory software can automatically update stock levels after each sale.
- Risks and Mitigations: The risk of technology failure or data loss can be mitigated by using cloud-based solutions, implementing regular backups, and having contingency plans in place.
- Impact and Implications: Investing in inventory technology can lead to significant improvements in accuracy, efficiency, reduced costs, and improved decision-making. This ultimately translates into increased profitability and reduced operational disruptions.
Conclusion: Reinforcing the Connection:
The integration of technology into inventory management is not merely an option but a necessity for small businesses aiming for efficient and accurate stocktaking. By leveraging available tools, businesses can transform their inventory processes, maximizing their resources and fostering growth.
Further Analysis: Examining Inventory Management Software in Greater Detail:
Inventory management software offers a range of features tailored to the needs of small businesses. These features often include:
- Real-time inventory tracking: Provides up-to-the-minute visibility into stock levels.
- Automated ordering: Triggers purchase orders when stock levels reach predefined thresholds.
- Sales forecasting: Predicts future demand based on historical data.
- Reporting and analysis: Provides detailed reports on inventory performance.
- Integration with POS systems: Synchronizes sales data with inventory levels.
- Barcode and RFID support: Facilitates efficient inventory counting and tracking.
- Multi-location support: Manages inventory across multiple locations.
Choosing the right software depends on your specific needs and budget. Research different options, considering factors such as scalability, features, ease of use, and integration with existing systems.
FAQ Section: Answering Common Questions About Inventory Taking:
-
Q: How often should I take inventory?
- A: The frequency depends on your business model and inventory turnover. Businesses with high turnover may need to take inventory more frequently, perhaps weekly or monthly, using cycle counting. Others may be able to manage with annual periodic counts.
-
Q: What if I find significant discrepancies?
- A: Investigate the cause of the discrepancies thoroughly. Check for damaged or lost items, review purchase orders and sales records, and adjust your inventory records accordingly. Use this experience to improve your inventory management processes.
-
Q: What's the best way to organize my inventory for counting?
- A: Organize your inventory logically by product category, location, or other relevant criteria. Clear labeling and organization significantly speeds up the counting process and reduces errors.
-
Q: How can I prevent inventory shrinkage?
- A: Implement strong security measures, regularly check for damaged or expired goods, and utilize technology to track inventory in real-time.
Practical Tips: Maximizing the Benefits of Efficient Inventory Management:
- Implement a robust inventory management system: This could involve utilizing inventory management software or even a simple spreadsheet system.
- Train your staff: Ensure your team understands the importance of accurate inventory and is proficient in using any inventory management tools.
- Regularly review your inventory data: Identify trends and patterns to optimize purchasing and pricing decisions.
- Conduct regular cycle counts: This helps to maintain accurate inventory levels throughout the year, rather than relying on infrequent, large-scale counts.
- Use barcodes or RFID tags: This allows for quick and accurate inventory counting, minimizing human error.
Final Conclusion: Wrapping Up with Lasting Insights:
Accurate and efficient inventory management is paramount for small business success. By implementing the strategies outlined in this guide, you can gain valuable control over your stock, optimize your purchasing decisions, improve customer satisfaction, and ultimately boost your bottom line. Remember that the key to a streamlined inventory process lies in meticulous planning, the judicious use of technology, and the commitment to ongoing process improvement.
Latest Posts
Related Post
Thank you for visiting our website which covers about What To Do When Taking Inventory In A Small Business . We hope the information provided has been useful to you. Feel free to contact us if you have any questions or need further assistance. See you next time and don't miss to bookmark.