What Is The Fill Rate Supply Chain
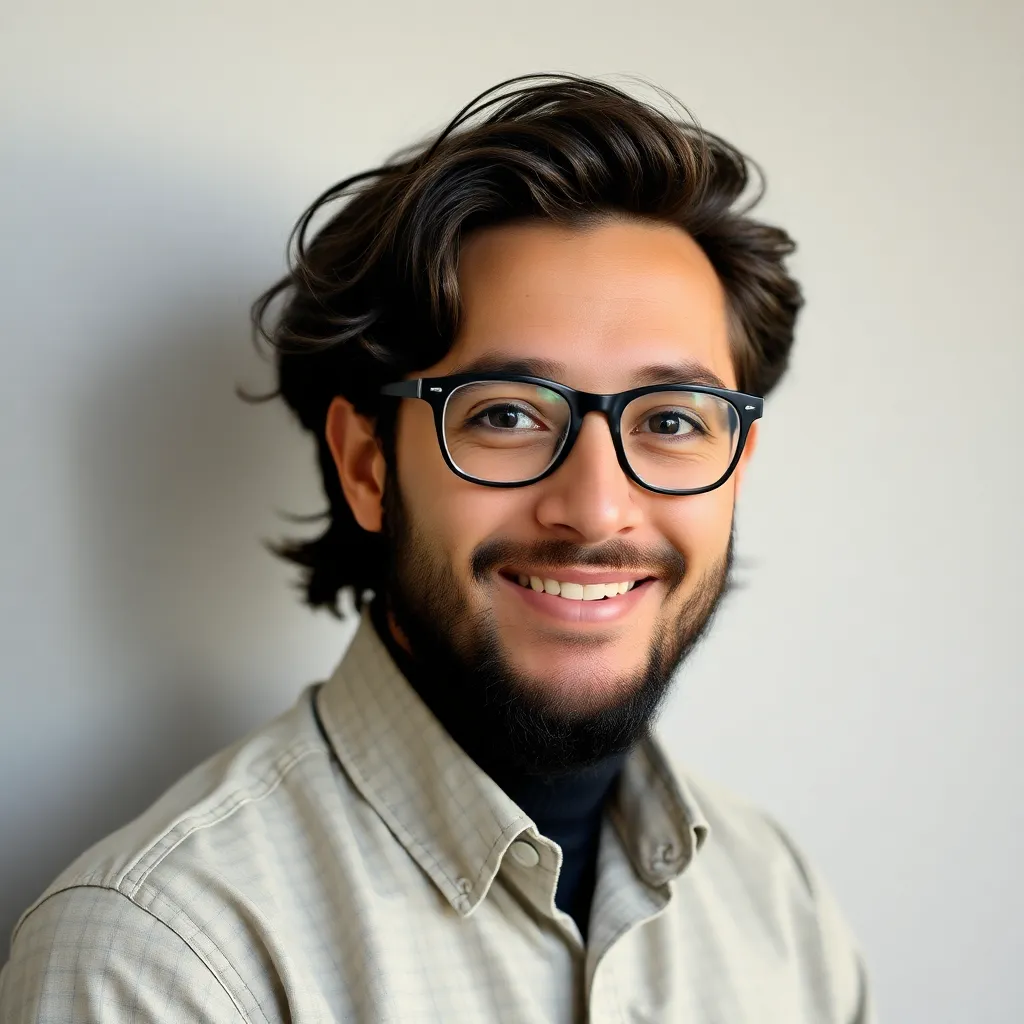
adminse
Apr 19, 2025 · 9 min read

Table of Contents
What if the future of successful businesses hinges on mastering fill rate in the supply chain?
Optimizing fill rate isn't just about meeting customer expectations; it's the cornerstone of a resilient and profitable supply chain.
Editor’s Note: This article on supply chain fill rate was published today, providing you with the latest insights and best practices in this crucial area of supply chain management. Understanding and improving your fill rate is essential for business success in today's dynamic market.
Why Supply Chain Fill Rate Matters:
Supply chain fill rate is a critical metric measuring a company's ability to meet customer demand from readily available inventory. It represents the percentage of customer orders fulfilled directly from existing stock, without backorders or delays. A high fill rate signifies efficiency, strong forecasting, and effective inventory management. Conversely, a low fill rate signals potential problems, including lost sales, dissatisfied customers, and damaged brand reputation. The implications extend beyond immediate sales; a consistently low fill rate can lead to decreased customer loyalty, higher operational costs (due to expedited shipping or backorder processing), and ultimately, reduced profitability. The importance of optimizing fill rate is amplified in industries with short product lifecycles, high demand volatility, or significant competition.
Overview: What This Article Covers
This article provides a comprehensive understanding of supply chain fill rate. We will delve into its definition, calculation, importance, factors influencing it, best practices for improvement, and the crucial relationship between fill rate and other key supply chain metrics. We will explore real-world examples and offer practical strategies to help businesses achieve and maintain a high fill rate.
The Research and Effort Behind the Insights
This article is based on extensive research, drawing from reputable sources including academic publications, industry reports, and case studies from leading companies across various sectors. The analysis incorporates data-driven insights and expert opinions to ensure accuracy and provide actionable recommendations.
Key Takeaways:
- Definition and Core Concepts: A clear explanation of fill rate, its calculation, and its significance in supply chain management.
- Factors Influencing Fill Rate: Identification of key internal and external factors impacting fill rate performance.
- Best Practices for Improvement: Practical strategies and techniques to enhance fill rate and optimize inventory management.
- Fill Rate and Other Key Metrics: Understanding the relationship between fill rate and other vital supply chain performance indicators.
- Case Studies and Examples: Real-world illustrations showcasing successful fill rate optimization strategies.
Smooth Transition to the Core Discussion:
Now that we understand the foundational importance of fill rate, let's delve into the specifics, examining its calculation, the factors affecting it, and proven methods to improve this critical metric.
Exploring the Key Aspects of Supply Chain Fill Rate:
1. Definition and Core Concepts:
Supply chain fill rate is calculated as the percentage of customer orders fulfilled from existing inventory. The formula is:
(Total Units Shipped / Total Units Ordered) * 100
For example, if a company receives 100 orders and ships 95 directly from stock, its fill rate is 95%. It's crucial to understand that this metric typically focuses on the order line level, meaning each individual item within an order is considered. A single backordered item within a multi-item order will negatively impact the overall fill rate.
2. Factors Influencing Fill Rate:
Several internal and external factors influence a company's fill rate. Understanding these factors is essential for effective improvement strategies.
- Demand Forecasting: Accurate demand forecasting is paramount. Inaccurate forecasts lead to either overstocking (tying up capital and increasing storage costs) or understocking (resulting in lost sales and dissatisfied customers). Sophisticated forecasting models, incorporating historical data, seasonality, and market trends, are crucial.
- Inventory Management: Effective inventory management systems are essential for maintaining optimal stock levels. This includes utilizing appropriate inventory control techniques such as Just-in-Time (JIT) or Economic Order Quantity (EOQ) to minimize holding costs while ensuring sufficient stock to meet demand.
- Supplier Relationships: Reliable and responsive suppliers are critical. Delays or disruptions from suppliers directly impact the availability of inventory and negatively affect fill rate. Strong supplier relationships, including collaborative planning, forecasting, and replenishment (CPFR), are essential.
- Production Capacity: Manufacturing bottlenecks or production inefficiencies can constrain the ability to replenish inventory, leading to lower fill rates. Effective capacity planning and process optimization are crucial for maintaining sufficient production output.
- Warehouse Management: Efficient warehouse operations are vital for accurate inventory tracking and timely order fulfillment. This includes optimizing warehouse layout, implementing robust inventory management systems (WMS), and ensuring efficient order picking and packing processes.
- Transportation and Logistics: Delays or disruptions in transportation and logistics can hinder timely delivery of goods, negatively affecting fill rate. Utilizing reliable transportation partners and optimizing logistics networks are essential.
- External Factors: External factors such as natural disasters, geopolitical instability, or economic downturns can also impact fill rate beyond the control of the company. Robust risk management strategies and contingency planning are necessary to mitigate these effects.
3. Best Practices for Improvement:
Improving supply chain fill rate requires a multifaceted approach:
- Invest in Advanced Forecasting Technologies: Employ sophisticated forecasting models that incorporate machine learning and AI to improve demand prediction accuracy.
- Implement Robust Inventory Management Systems: Utilize advanced inventory management software to provide real-time visibility into inventory levels, track stock movements, and optimize inventory replenishment strategies.
- Strengthen Supplier Relationships: Foster strong partnerships with key suppliers through collaborative planning, forecasting, and replenishment (CPFR) initiatives. Establish clear communication channels and performance metrics.
- Optimize Production Processes: Identify and eliminate production bottlenecks to increase efficiency and ensure timely replenishment of inventory.
- Improve Warehouse Management: Implement efficient warehouse management systems (WMS) to streamline inventory tracking, order picking, and packing processes.
- Diversify Supplier Base: Reduce reliance on single suppliers to mitigate risks associated with supply chain disruptions.
- Implement Safety Stock Strategies: Maintain appropriate safety stock levels to buffer against unforeseen demand fluctuations or supply chain disruptions. However, carefully balance safety stock levels to avoid excessive inventory holding costs.
- Improve Data Visibility and Analysis: Leverage data analytics to gain real-time insights into inventory levels, demand patterns, and potential supply chain disruptions. Use this data to proactively address potential issues.
4. Fill Rate and Other Key Metrics:
Fill rate is closely related to other key supply chain metrics, such as:
- Inventory Turnover: High fill rate generally correlates with efficient inventory turnover, indicating efficient inventory management.
- Order Cycle Time: A high fill rate often indicates shorter order cycle times, leading to faster delivery and enhanced customer satisfaction.
- Customer Service Level: High fill rate is directly linked to higher customer service levels, resulting in increased customer satisfaction and loyalty.
- Stockout Rate: Fill rate is the inverse of the stockout rate. A high fill rate indicates a low stockout rate.
- Backorder Rate: A high fill rate indicates a low backorder rate, showing efficient order fulfillment.
Exploring the Connection Between Safety Stock and Fill Rate:
The relationship between safety stock and fill rate is crucial. Safety stock acts as a buffer against demand variability and supply chain disruptions. Higher safety stock levels generally lead to higher fill rates, but at the cost of increased inventory holding costs. The optimal safety stock level needs to be carefully determined by considering the trade-off between improved fill rate and increased inventory costs. This often involves sophisticated inventory optimization techniques and statistical analysis.
Key Factors to Consider:
- Roles and Real-World Examples: Companies like Amazon and Walmart, known for their high fill rates, demonstrate the power of advanced forecasting, efficient logistics, and robust inventory management systems. Their success is a testament to the importance of prioritizing fill rate optimization.
- Risks and Mitigations: Risks associated with low fill rates include lost sales, damaged customer relationships, and decreased profitability. Mitigation strategies include investing in advanced forecasting, enhancing supplier relationships, and implementing robust inventory management systems.
- Impact and Implications: The impact of low fill rates can be significant, leading to decreased market share, loss of competitive advantage, and ultimately, business failure. Therefore, proactive management and optimization of fill rate are critical for long-term sustainability.
Conclusion: Reinforcing the Connection:
The connection between safety stock and fill rate highlights the complexity of inventory management. Striking the right balance between sufficient stock to meet customer demand and minimizing unnecessary inventory holding costs is a constant challenge. Effective strategies involve utilizing advanced forecasting techniques, strong supplier relationships, and efficient warehouse management systems.
Further Analysis: Examining Safety Stock in Greater Detail:
Safety stock calculations involve statistical analysis, considering factors such as demand variability, lead time variability, and desired service level. Different inventory management models, such as the normal distribution model or the Poisson distribution model, are employed to determine the optimal safety stock level. The choice of model depends on the specific characteristics of the product and demand patterns.
FAQ Section: Answering Common Questions About Supply Chain Fill Rate:
- What is supply chain fill rate? Supply chain fill rate is the percentage of customer orders fulfilled directly from existing inventory.
- How is fill rate calculated? (Total Units Shipped / Total Units Ordered) * 100
- Why is fill rate important? High fill rate leads to improved customer satisfaction, reduced backorders, enhanced operational efficiency, and increased profitability.
- How can I improve my fill rate? By improving demand forecasting, optimizing inventory management, strengthening supplier relationships, and enhancing warehouse operations.
- What is the ideal fill rate? The ideal fill rate varies depending on the industry, but generally, a higher fill rate (above 95%) indicates excellent performance.
Practical Tips: Maximizing the Benefits of a High Fill Rate:
- Regularly review and refine your demand forecasting models. Incorporate new data and adjust parameters as needed.
- Implement a robust inventory management system with real-time visibility. Track inventory levels, monitor stock movements, and automate replenishment processes.
- Foster strong collaborative relationships with your suppliers. Share forecasts, collaborate on inventory management, and proactively address potential supply chain disruptions.
- Optimize your warehouse layout and operations. Streamline order picking and packing processes to reduce lead times and improve efficiency.
- Regularly analyze your fill rate performance and identify areas for improvement. Use data-driven insights to make informed decisions.
Final Conclusion: Wrapping Up with Lasting Insights:
Supply chain fill rate is a critical performance indicator that directly impacts customer satisfaction, operational efficiency, and profitability. By implementing the strategies outlined in this article, businesses can significantly improve their fill rate, enhancing their competitiveness and driving long-term success. Maintaining a high fill rate isn't merely a metric; it's a reflection of a well-managed and resilient supply chain, ready to meet the ever-evolving demands of the market.
Latest Posts
Related Post
Thank you for visiting our website which covers about What Is The Fill Rate Supply Chain . We hope the information provided has been useful to you. Feel free to contact us if you have any questions or need further assistance. See you next time and don't miss to bookmark.