What Is Gearing Definition Hows Its Measured And Example
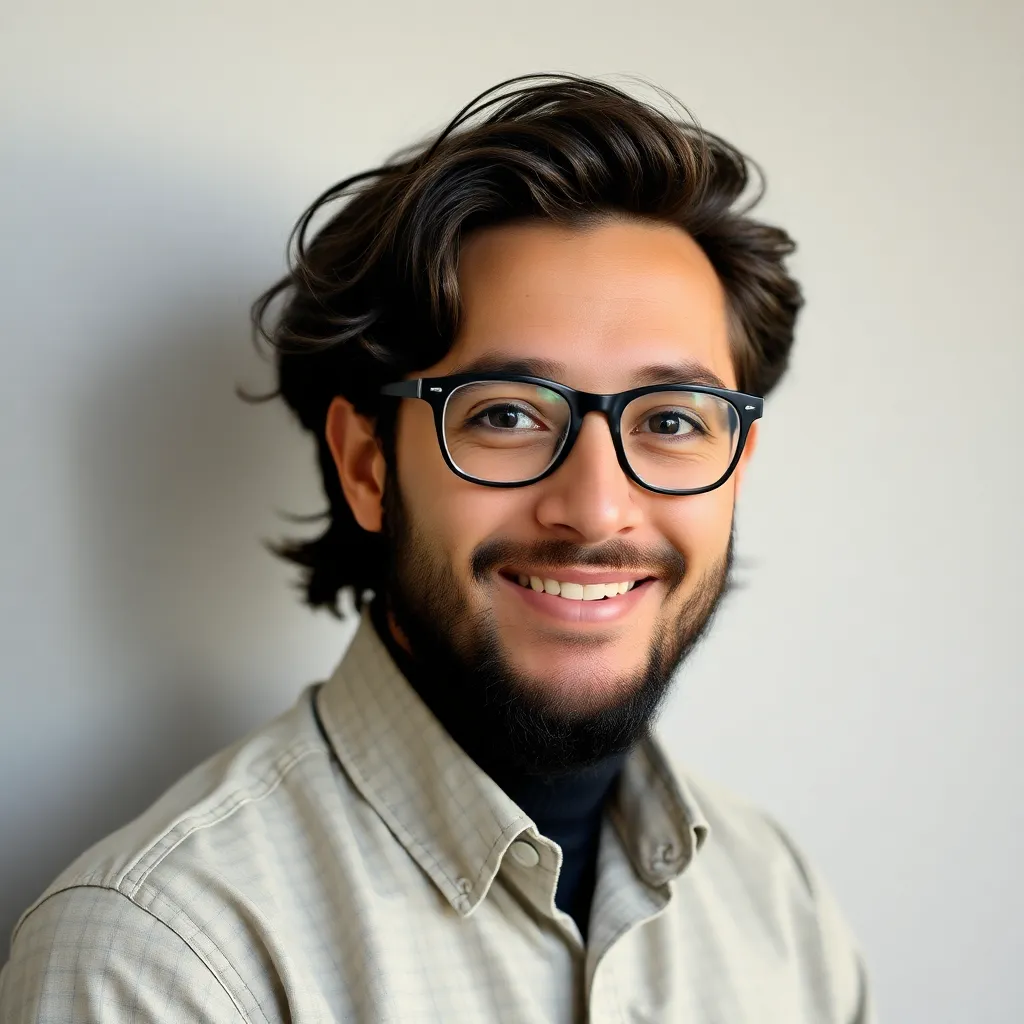
adminse
Apr 23, 2025 · 9 min read

Table of Contents
Understanding Gearing: Definition, Measurement, and Real-World Examples
What if the optimal performance of countless machines hinges on a precise understanding of gearing? This fundamental mechanical principle is the backbone of countless applications, from simple hand tools to complex industrial machinery.
Editor’s Note: This article on gearing provides a comprehensive overview of its definition, measurement, and real-world applications. Updated with the latest insights, it aims to serve as a valuable resource for engineers, students, and anyone interested in the mechanics of power transmission.
Why Gearing Matters: Relevance, Practical Applications, and Industry Significance
Gearing is a crucial element in mechanical engineering, enabling the efficient transmission of power and torque between rotating shafts. Its significance stems from its ability to alter speed and torque ratios, allowing for precise control over machinery performance. From the tiny gears in a wristwatch to the massive gears in a wind turbine, gearing finds application across diverse industries, including automotive, aerospace, robotics, and manufacturing. The effective design and implementation of gearing systems directly impact efficiency, durability, and the overall functionality of countless machines. Understanding gearing's principles is essential for optimizing machine design, improving energy efficiency, and ensuring reliable operation. This includes considerations of gear types, materials, manufacturing processes, and lubrication techniques.
Overview: What This Article Covers
This article provides a detailed exploration of gearing, covering its fundamental definition, different types of gears, methods of measuring gear ratios and efficiency, and illustrative examples from various industries. Readers will gain a clear understanding of the importance of gearing in mechanical systems and how its principles are applied to achieve desired performance characteristics.
The Research and Effort Behind the Insights
This article is the product of extensive research, drawing upon established mechanical engineering principles and incorporating information from reputable textbooks, technical journals, and industry standards. Numerous real-world examples are included to illustrate the practical applications of gearing across various sectors. The information presented aims to provide accurate and reliable insights for a wide audience.
Key Takeaways:
- Definition and Core Concepts: A precise definition of gearing and its fundamental principles.
- Gear Types and Characteristics: An overview of various gear types (spur, helical, bevel, worm) and their respective applications.
- Gear Ratio Calculation: Methods for determining the gear ratio and its impact on speed and torque.
- Gear Efficiency: Factors influencing gear efficiency and techniques for optimization.
- Real-World Applications: Numerous examples illustrating the practical applications of gearing in various industries.
- Challenges and Considerations: Common challenges encountered in gear design and strategies for mitigation.
Smooth Transition to the Core Discussion
Having established the importance of gearing, let's delve into a detailed exploration of its key aspects, beginning with a clear definition and progressing to its diverse applications and challenges.
Exploring the Key Aspects of Gearing
1. Definition and Core Concepts:
Gearing, in its simplest form, refers to a mechanism that utilizes meshed teeth on rotating components (gears) to transmit rotational motion and torque from one shaft to another. This process allows for modification of rotational speed and torque, a crucial aspect in many mechanical systems. The fundamental principle is based on the engagement of precisely shaped teeth, ensuring smooth and efficient power transmission. The interaction of these teeth adheres to specific geometric principles to maintain consistent contact and minimize wear.
2. Gear Types and Characteristics:
Several types of gears exist, each designed to accommodate specific needs based on shaft arrangement and power transmission requirements. The most common types include:
- Spur Gears: These gears have straight teeth parallel to the axis of rotation and are suitable for parallel shafts. They are relatively simple to manufacture but can be noisy at high speeds.
- Helical Gears: Featuring helical teeth, these gears provide smoother and quieter operation compared to spur gears, especially at high speeds. They are often preferred for applications demanding quieter and more efficient transmission.
- Bevel Gears: Used for transmitting power between intersecting shafts, bevel gears come in various types, including straight bevel, spiral bevel, and hypoid gears. Their angled teeth allow for efficient power transmission at angles.
- Worm Gears: Consisting of a worm (screw-like gear) and a worm wheel, these gears are particularly useful for high gear ratios and self-locking capabilities. They offer quiet operation but have lower efficiency compared to other gear types.
3. Gear Ratio Calculation:
The gear ratio is a fundamental parameter that determines the relationship between the input and output speeds and torques of a gearing system. It's defined as the ratio of the number of teeth on the driven gear (output) to the number of teeth on the driving gear (input).
Gear Ratio = (Number of teeth on driven gear) / (Number of teeth on driving gear)
A gear ratio greater than 1 indicates a speed reduction (increase in torque), while a ratio less than 1 signifies a speed increase (reduction in torque). This relationship is crucial in selecting appropriate gearing for specific applications, such as achieving the required speed and torque for a motor driving a load.
4. Gear Efficiency:
Gear efficiency represents the ratio of output power to input power. While ideal gears would have 100% efficiency, real-world gears experience losses due to friction, tooth wear, and lubrication deficiencies. Factors affecting gear efficiency include:
- Gear Design: The geometry of the teeth, tooth profile, and contact ratio influence efficiency.
- Manufacturing Precision: Accurate manufacturing minimizes friction and wear, improving efficiency.
- Lubrication: Proper lubrication reduces friction and wear, leading to higher efficiency.
- Material Properties: The material's strength, hardness, and wear resistance impact efficiency.
5. Real-World Applications:
The applications of gearing are incredibly diverse and span various industries:
- Automotive Industry: Gearboxes in vehicles use gearing to provide different speed and torque ranges, optimizing engine performance for various driving conditions.
- Aerospace Industry: Aircraft and spacecraft utilize gearing in flight control systems, landing gear mechanisms, and propulsion systems.
- Robotics: Robots rely on gearing for precise and controlled movement of their limbs and joints.
- Manufacturing: Numerous machines in manufacturing use gearing for power transmission, speed control, and precise positioning.
- Wind Turbines: Large gears in wind turbines transmit the rotational power generated by the blades to the generator.
- Clocks and Watches: Precisely engineered gears ensure accurate timekeeping in clocks and watches.
6. Challenges and Considerations:
Designing and implementing effective gearing systems involves addressing several challenges:
- Backlash: The clearance between meshing teeth can cause backlash, leading to inaccuracies and vibrations.
- Wear and Tear: Friction and wear can degrade gear performance over time, reducing efficiency and requiring maintenance.
- Noise and Vibration: Improperly designed or worn gears can generate excessive noise and vibrations.
- Lubrication: Maintaining proper lubrication is crucial to prevent wear and ensure efficient operation.
- Material Selection: Choosing appropriate materials for the gears based on the operating conditions is essential for durability.
Closing Insights: Summarizing the Core Discussion
Gearing is a fundamental mechanical principle vital for efficient power transmission and speed/torque control in a wide array of machines. Understanding gear types, ratio calculations, efficiency considerations, and potential challenges is crucial for effective design and implementation. The selection of appropriate gear types and materials, coupled with proper maintenance, ensures optimal performance and longevity.
Exploring the Connection Between Gear Material and Gearing Efficiency
The choice of gear material significantly impacts gearing efficiency. This connection stems from the material's properties influencing friction, wear, and strength characteristics.
Key Factors to Consider:
- Roles and Real-World Examples: Steel, commonly used for its strength and durability, provides high efficiency in many applications. However, plastics are employed in some situations due to their low cost and noise-reducing properties, albeit with lower efficiency.
- Risks and Mitigations: Using materials with poor wear resistance can lead to increased friction and reduced efficiency. Surface treatments like nitriding or carburizing can mitigate this risk by enhancing surface hardness.
- Impact and Implications: The material's influence extends to the overall lifespan and maintenance requirements of the gearing system. Choosing a high-performance material leads to longer operational life and less downtime.
Conclusion: Reinforcing the Connection
The gear material selection is a crucial design parameter that directly influences efficiency, durability, and the overall performance of the gearing system. Careful consideration of material properties is essential to optimize the gearing system's efficiency and longevity.
Further Analysis: Examining Gear Manufacturing Processes in Greater Detail
Gear manufacturing employs diverse processes to achieve precise tooth geometry and surface finish. These processes significantly impact gear quality, efficiency, and lifespan. Methods include hobbing, shaping, broaching, and grinding, each offering varying levels of precision and cost-effectiveness. Advanced manufacturing techniques like 3D printing are also gaining traction, offering flexibility in design and material selection.
FAQ Section: Answering Common Questions About Gearing
-
Q: What is a gear ratio and how is it calculated?
- A: A gear ratio is the ratio of the number of teeth on the driven gear to the number of teeth on the driving gear. It's calculated by dividing the number of teeth on the driven gear by the number of teeth on the driving gear.
-
Q: What are the different types of gears?
- A: Common types include spur, helical, bevel, and worm gears, each suitable for specific shaft arrangements and applications.
-
Q: How does gear material affect efficiency?
- A: Gear material impacts efficiency through its influence on friction, wear, and strength. Harder materials generally lead to higher efficiency.
-
Q: What are some common problems with gears?
- A: Backlash, wear, noise, and vibration are common issues that can be mitigated through proper design, material selection, and maintenance.
Practical Tips: Maximizing the Benefits of Gearing
- Understand Gear Types: Select the appropriate gear type based on the application's requirements.
- Calculate Gear Ratio: Accurately determine the required gear ratio for desired speed and torque.
- Choose Appropriate Materials: Select materials that offer high strength, hardness, and wear resistance.
- Ensure Proper Lubrication: Use appropriate lubricants to minimize friction and wear.
- Regular Inspection and Maintenance: Regularly inspect gears for wear and tear and perform necessary maintenance.
Final Conclusion: Wrapping Up with Lasting Insights
Gearing, a fundamental mechanical principle, underpins countless machines and systems. By understanding its definition, measurement, different types, and the influence of material selection, engineers and designers can optimize performance, efficiency, and longevity. The continued development and refinement of gear technology will undoubtedly play a key role in future innovations across many sectors.
Latest Posts
Latest Posts
-
Guaranteed Income Bond Gib Definition
Apr 23, 2025
-
Guaranteed Cost Premium Definition
Apr 23, 2025
-
Guaranteed Bond Definition
Apr 23, 2025
-
Growth Recession Definition
Apr 23, 2025
-
Growth Rates Formula How To Calculate And Definition
Apr 23, 2025
Related Post
Thank you for visiting our website which covers about What Is Gearing Definition Hows Its Measured And Example . We hope the information provided has been useful to you. Feel free to contact us if you have any questions or need further assistance. See you next time and don't miss to bookmark.