What Is A Lean Supply Chain
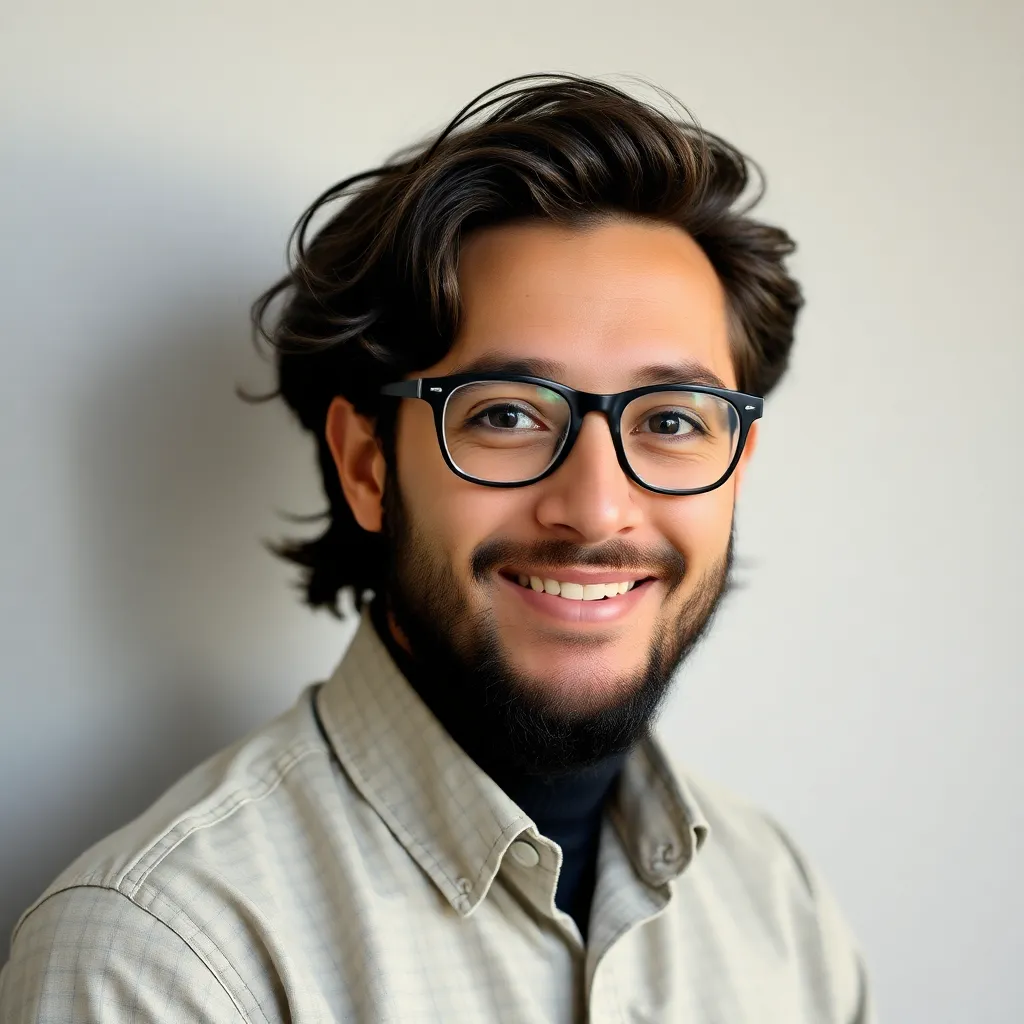
adminse
Apr 19, 2025 · 9 min read

Table of Contents
Unveiling the Lean Supply Chain: Efficiency, Agility, and Value Creation
What if the future of manufacturing and distribution hinges on embracing lean principles in the supply chain? This transformative approach is already streamlining operations, reducing waste, and delivering exceptional value to businesses across diverse sectors.
Editor’s Note: This article on lean supply chains provides a comprehensive overview of this crucial business strategy. We've combined academic research, industry best practices, and real-world examples to offer a practical guide for businesses seeking to optimize their supply chain operations.
Why Lean Supply Chains Matter:
In today's fiercely competitive global marketplace, efficiency and responsiveness are paramount. Lean supply chains offer a powerful framework for achieving these goals. By minimizing waste, maximizing value, and fostering continuous improvement, businesses can gain a significant competitive edge. The benefits extend beyond mere cost reduction; they encompass enhanced customer satisfaction, improved product quality, and increased profitability. The principles of lean thinking, originally developed in manufacturing, are now widely adopted across various industries, from automotive and electronics to healthcare and food processing, showcasing their broad applicability and transformative potential. The application of lean principles directly contributes to reduced lead times, improved inventory management, and enhanced overall supply chain resilience. This translates to lower costs, faster delivery, and greater customer satisfaction – key ingredients for sustained success in today's dynamic business environment.
Overview: What This Article Covers:
This article explores the core principles of a lean supply chain, its key components, and the methodologies used to implement it effectively. We will delve into specific techniques, real-world examples, and potential challenges, providing actionable insights for businesses at various stages of their lean journey. Readers will gain a comprehensive understanding of how to build a lean supply chain that is both efficient and agile, capable of responding effectively to market demands and disruptions.
The Research and Effort Behind the Insights:
This article is the culmination of extensive research, drawing upon established academic literature, industry reports, case studies from leading companies, and expert interviews. We have meticulously analyzed various methodologies and best practices to provide a comprehensive and up-to-date perspective on lean supply chain management. The information presented is intended to be both informative and practical, offering readers actionable insights that can be directly applied to their own organizations.
Key Takeaways:
- Definition and Core Concepts: A clear understanding of what constitutes a lean supply chain and its foundational principles.
- Implementing Lean Principles: Practical steps and methodologies for implementing lean thinking within a supply chain.
- Waste Reduction Techniques: Identifying and eliminating various forms of waste throughout the supply chain.
- Technology's Role: Exploring the role of technology in supporting lean initiatives.
- Challenges and Best Practices: Addressing common challenges and highlighting successful strategies for overcoming them.
- Measuring Success: Defining key performance indicators (KPIs) to track progress and measure the effectiveness of lean initiatives.
Smooth Transition to the Core Discussion:
With a clear understanding of the importance of lean supply chains, let's delve into the core principles and practical applications of this transformative approach.
Exploring the Key Aspects of a Lean Supply Chain:
1. Definition and Core Concepts:
A lean supply chain is a management philosophy focused on eliminating waste and maximizing value throughout the entire supply chain, from raw material sourcing to final product delivery. It builds upon the principles of lean manufacturing, emphasizing continuous improvement (Kaizen), waste reduction (Muda), and value stream mapping. The goal is to create a highly efficient, flexible, and responsive supply chain capable of meeting customer demands effectively while minimizing costs. Central to this is the identification and elimination of seven types of waste: Overproduction, Waiting, Transportation, Over-processing, Inventory, Motion, and Defects (often remembered by the acronym “TIMWOOD”).
2. Implementing Lean Principles:
Implementing a lean supply chain is an iterative process requiring a holistic approach. It begins with a thorough assessment of the existing supply chain, identifying bottlenecks and areas of inefficiency. Key methodologies include:
- Value Stream Mapping (VSM): A visual tool used to map the entire flow of materials and information, identifying areas of waste and opportunities for improvement.
- 5S Methodology: A workplace organization method focusing on Sort, Set in Order, Shine, Standardize, and Sustain, creating a more efficient and safer work environment.
- Kaizen Events: Short, focused workshops aimed at identifying and implementing quick, impactful improvements.
- Kanban: A visual signaling system used to manage inventory and production flow, ensuring just-in-time delivery.
- Poka-Yoke: Error-proofing techniques designed to prevent defects from occurring in the first place.
3. Waste Reduction Techniques:
Identifying and eliminating waste is fundamental to a lean supply chain. Specific techniques include:
- Reducing Inventory: Implementing just-in-time (JIT) inventory management systems to minimize storage costs and reduce the risk of obsolescence.
- Optimizing Transportation: Streamlining logistics and transportation routes to reduce lead times and transportation costs.
- Improving Production Processes: Eliminating unnecessary steps and improving efficiency in manufacturing and assembly processes.
- Reducing Defects: Implementing quality control measures to minimize errors and prevent defects from reaching the customer.
- Minimizing Waiting Time: Improving workflow and scheduling to reduce waiting times for materials, information, and processes.
4. Technology's Role:
Technology plays a crucial role in supporting lean initiatives. This includes:
- Enterprise Resource Planning (ERP) Systems: Integrated systems that manage various aspects of the supply chain, providing real-time visibility and data-driven decision-making.
- Supply Chain Management (SCM) Software: Specialized software solutions designed to optimize logistics, inventory management, and transportation.
- Radio Frequency Identification (RFID): Tracking technology used to monitor the movement of goods throughout the supply chain.
- Blockchain Technology: Enhancing transparency and traceability within the supply chain, improving security and reducing fraud.
- Artificial Intelligence (AI) and Machine Learning (ML): Utilizing data analytics and predictive modeling to anticipate demand, optimize inventory levels, and improve forecasting accuracy.
5. Challenges and Best Practices:
Implementing a lean supply chain presents several challenges, including:
- Resistance to Change: Overcoming resistance from employees and stakeholders accustomed to traditional processes.
- Data Integration: Integrating data from various sources across the supply chain.
- Supplier Collaboration: Fostering strong relationships and collaboration with suppliers.
- Technology Implementation: Successfully integrating and utilizing technology to support lean initiatives.
- Measuring Success: Defining and tracking appropriate KPIs to monitor progress and measure the effectiveness of lean efforts.
Best practices for overcoming these challenges include:
- Strong Leadership and Commitment: Top-down support and commitment from leadership is crucial for successful implementation.
- Employee Involvement: Involving employees in the process to foster buy-in and ownership.
- Phased Implementation: Implementing lean principles in stages, starting with pilot projects before wider rollouts.
- Continuous Improvement: Embracing a culture of continuous improvement and ongoing refinement.
- Collaboration and Communication: Maintaining open communication and collaboration throughout the supply chain.
6. Measuring Success:
Key Performance Indicators (KPIs) are essential for tracking progress and measuring the effectiveness of lean initiatives. These include:
- Inventory Turnover: Measuring the efficiency of inventory management.
- Lead Time: Measuring the time it takes to deliver a product or service.
- On-Time Delivery: Measuring the percentage of orders delivered on time.
- Defect Rate: Measuring the number of defective products or services.
- Customer Satisfaction: Measuring customer satisfaction with the product or service and the overall supply chain experience.
- Cost Reduction: Tracking the reduction in costs associated with inventory, transportation, and other supply chain activities.
Closing Insights: Summarizing the Core Discussion:
A lean supply chain is more than just a cost-cutting strategy; it is a philosophy that emphasizes continuous improvement, waste reduction, and value creation. By implementing the principles and methodologies outlined above, businesses can build a highly efficient, responsive, and resilient supply chain that is capable of meeting customer demands while achieving significant cost savings and competitive advantage. The successful implementation of lean principles requires a long-term commitment, strong leadership, and the active participation of all stakeholders throughout the supply chain.
Exploring the Connection Between Technology and Lean Supply Chains:
Technology plays a transformative role in enabling and enhancing lean supply chain principles. It allows for greater visibility, improved data analysis, and enhanced automation, all of which are critical for optimizing efficiency and reducing waste.
Key Factors to Consider:
- Roles and Real-World Examples: Technology such as ERP systems, RFID tracking, and AI-powered predictive analytics provide real-time data visibility across the entire supply chain. Companies like Toyota have leveraged technology to achieve exceptional levels of just-in-time manufacturing and inventory management.
- Risks and Mitigations: High initial investment costs, data security concerns, and the need for robust IT infrastructure are potential risks. Mitigations include carefully planning technology investments, implementing robust cybersecurity measures, and investing in employee training.
- Impact and Implications: Improved forecasting accuracy, reduced lead times, optimized inventory levels, and enhanced collaboration with suppliers are significant implications. This ultimately leads to increased customer satisfaction, reduced costs, and enhanced business agility.
Conclusion: Reinforcing the Connection:
The synergy between technology and lean supply chain principles is undeniable. Technology empowers businesses to implement lean methodologies more effectively, leading to substantial improvements in efficiency, agility, and profitability. By embracing technology and adopting a data-driven approach, businesses can unlock the full potential of lean thinking and achieve sustainable competitive advantage.
Further Analysis: Examining the Role of Supplier Relationships in Lean Supply Chains:
Strong supplier relationships are paramount in a lean supply chain. Collaboration and trust between a company and its suppliers are essential for ensuring the timely delivery of high-quality materials and components.
FAQ Section: Answering Common Questions About Lean Supply Chains:
- What is a lean supply chain? A lean supply chain is a management philosophy aimed at eliminating waste and maximizing value throughout the entire supply chain.
- What are the benefits of a lean supply chain? Benefits include reduced costs, improved efficiency, increased customer satisfaction, enhanced agility, and improved resilience.
- How can I implement a lean supply chain in my business? Start with a thorough assessment of your current supply chain, identify areas of waste, and implement lean methodologies like VSM, 5S, and Kaizen.
- What technology can support a lean supply chain? ERP systems, SCM software, RFID, blockchain, AI, and ML are examples of technologies that can support lean initiatives.
- What are the key challenges of implementing a lean supply chain? Challenges include resistance to change, data integration issues, and the need for strong supplier relationships.
Practical Tips: Maximizing the Benefits of a Lean Supply Chain:
- Start with Value Stream Mapping: Visualize your current supply chain to identify bottlenecks and areas of waste.
- Prioritize Waste Reduction: Focus on eliminating the most significant forms of waste first.
- Embrace Continuous Improvement: Implement a culture of continuous improvement and ongoing refinement.
- Foster Collaboration: Build strong relationships with suppliers and internal teams.
- Utilize Technology: Leverage technology to enhance visibility, data analysis, and automation.
- Measure Your Progress: Track key performance indicators (KPIs) to monitor progress and measure success.
Final Conclusion: Wrapping Up with Lasting Insights:
The lean supply chain represents a paradigm shift in how businesses manage their operations. By focusing on efficiency, waste reduction, and continuous improvement, companies can achieve a significant competitive advantage in today's dynamic market. Embracing lean principles, coupled with strategic technology adoption and a commitment to ongoing improvement, will ultimately lead to increased profitability, enhanced customer satisfaction, and a more resilient and sustainable business model. The journey towards a lean supply chain is ongoing, requiring continuous adaptation and a commitment to excellence.
Latest Posts
Related Post
Thank you for visiting our website which covers about What Is A Lean Supply Chain . We hope the information provided has been useful to you. Feel free to contact us if you have any questions or need further assistance. See you next time and don't miss to bookmark.