What Bureau Does Toyota Pull
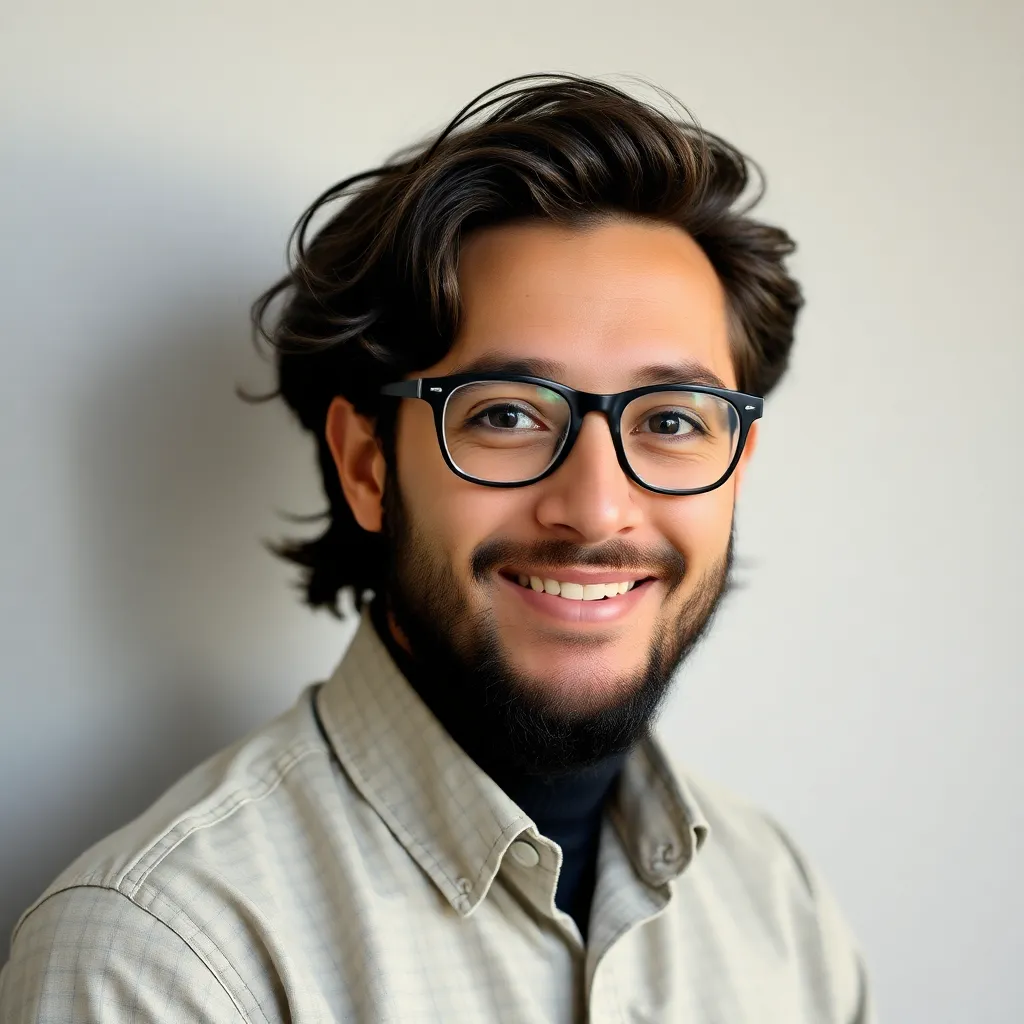
adminse
Apr 17, 2025 · 7 min read

Table of Contents
Unveiling Toyota's Bureaucratic Powerhouse: A Deep Dive into its Operational Structure
What if the success of a global automotive giant hinges on a finely tuned bureaucratic machine? Toyota's operational excellence isn't merely about efficient production lines; it's a testament to a meticulously crafted internal structure that drives innovation and ensures quality.
Editor's Note: This article provides an in-depth analysis of Toyota's organizational structure, exploring its key components and the role they play in the company's remarkable success. Updated information and insights are incorporated to reflect the current state of Toyota's operations.
Why Toyota's Bureaucracy Matters:
Toyota's reputation isn't solely built on its reliable vehicles; it's also rooted in its highly efficient and effective organizational structure. This intricate system, often described as a sophisticated bureaucracy, ensures consistent quality, streamlined processes, and continuous improvement across its global operations. Understanding this bureaucratic framework is crucial for comprehending Toyota's enduring success and its impact on the automotive industry. The impact extends beyond manufacturing, influencing supply chain management, R&D, marketing, and even human resource strategies globally.
Overview: What This Article Covers:
This article dissects Toyota's organizational structure, going beyond surface-level descriptions. We'll examine its key elements: the Toyota Production System (TPS), the role of kaizen, its hierarchical structure, decision-making processes, and the importance of standardization and communication within this system. Further, we'll analyze the interconnectedness between various departments and how they contribute to the overall operational efficiency. Finally, we'll explore both the strengths and potential weaknesses inherent in this approach.
The Research and Effort Behind the Insights:
This analysis draws upon extensive research, including academic papers on organizational management, case studies of Toyota's operations, and reports from industry analysts. We've analyzed Toyota's public statements, internal documents (where accessible), and secondary sources to paint a comprehensive picture of the company's internal workings. The goal is to provide a balanced and data-driven understanding of Toyota's bureaucratic system.
Key Takeaways:
- Toyota Production System (TPS): A deep dive into the foundational principles of lean manufacturing and its impact on efficiency.
- Kaizen and Continuous Improvement: Exploring the culture of continuous improvement and its role in maintaining competitiveness.
- Hierarchical Structure and Decision-Making: Examining Toyota's organizational chart and the processes involved in strategic and operational decision-making.
- Standardization and Communication: Analyzing the importance of standardized processes and effective communication in maintaining operational excellence.
- Global Coordination and Adaptation: Understanding how Toyota adapts its bureaucratic system to different regional contexts and markets.
Smooth Transition to the Core Discussion:
Toyota's success is not accidental; it's a direct result of its carefully constructed organizational structure. Let's delve into the specifics of this system and explore its various components.
Exploring the Key Aspects of Toyota's Organizational Structure:
1. The Toyota Production System (TPS): The Foundation of Efficiency:
TPS, the backbone of Toyota's manufacturing prowess, is a lean manufacturing methodology focused on eliminating waste and maximizing efficiency. It's characterized by several key principles:
- Just-in-Time (JIT) Inventory: Minimizing inventory by producing only what's needed, when it's needed. This reduces storage costs, minimizes waste from obsolete stock, and improves responsiveness to changing demand.
- Jidoka (Autonomation): Empowering workers to stop the production line if a problem is detected. This proactive approach prevents defects from propagating further down the line.
- Kaizen (Continuous Improvement): A culture of continuous improvement driven by employee suggestions and data-driven analysis. This ongoing refinement ensures that processes are constantly being optimized.
- Value Stream Mapping: A visual representation of the entire production process, allowing for identification of bottlenecks and areas for improvement.
2. Kaizen: The Engine of Continuous Improvement:
Kaizen, meaning "change for the better," is deeply ingrained in Toyota's culture. It's not merely a program; it's a philosophy that encourages every employee to identify and suggest improvements to processes. This bottom-up approach ensures that even small, incremental changes can lead to significant improvements in efficiency and quality over time. Toyota's success hinges on its ability to gather and implement these suggestions effectively, fostering a culture of continuous innovation and learning.
3. Hierarchical Structure and Decision-Making:
Toyota's organizational structure is hierarchical, with clear lines of authority and responsibility. This structure provides stability and ensures accountability. However, decision-making isn't solely top-down. Toyota empowers its employees at all levels to contribute to decision-making, particularly in areas related to process improvement. This blend of hierarchical structure and employee empowerment allows for both efficient execution and innovative solutions. Information flows both vertically and horizontally, ensuring that relevant data reaches the appropriate decision-makers.
4. Standardization and Communication:
Standardization of processes is crucial to Toyota's operational excellence. Standardized procedures ensure consistent quality and reduce variability. However, this standardization isn't rigid; it provides a foundation upon which continuous improvement can be built. Effective communication channels are equally important, ensuring that information flows seamlessly throughout the organization, facilitating collaboration and coordinated action. This communication network is crucial for the quick dissemination of kaizen suggestions and for addressing challenges promptly.
5. Global Coordination and Adaptation:
Toyota's global operations require a sophisticated system for coordinating activities across different regions and markets. While the core principles of TPS remain consistent, Toyota adapts its approach to local conditions, considering cultural factors, regulatory requirements, and consumer preferences. This ability to balance global standardization with local adaptation is a key factor in Toyota's international success. The bureaucratic structure allows for regional autonomy while maintaining a strong central control over core strategies and quality standards.
Exploring the Connection Between Lean Principles and Toyota's Bureaucracy:
Lean principles, embodied in TPS, are intrinsically linked to Toyota's bureaucratic structure. The bureaucracy provides the framework for implementing and sustaining lean practices. The hierarchical structure ensures accountability for implementing lean initiatives, while standardized processes provide a foundation for continuous improvement. The meticulous record-keeping and data analysis, typical of a bureaucratic system, are crucial for identifying areas for improvement and tracking progress in lean initiatives.
Key Factors to Consider:
- Roles and Real-World Examples: The different roles within Toyota's bureaucracy, from shop-floor workers to senior management, play specific parts in implementing and improving lean principles. Examples of successful kaizen implementations showcase the impact of this collaborative approach.
- Risks and Mitigations: Potential risks associated with Toyota's bureaucratic approach include rigidity, inflexibility, and resistance to change. However, Toyota mitigates these risks through ongoing training, employee empowerment, and a commitment to continuous improvement.
- Impact and Implications: The impact of Toyota's bureaucratic system is evident in its consistently high-quality products, efficient operations, and strong market position. It's a model for many other organizations seeking to improve efficiency and productivity.
Conclusion: Reinforcing the Connection:
Toyota's success is a powerful testament to the effective implementation of a well-structured bureaucracy. Its system, while seemingly rigid, incorporates elements of flexibility and employee empowerment, facilitating continuous improvement and adaptation. The interplay between lean principles and bureaucratic structure underscores Toyota's ability to blend efficiency with innovation.
Further Analysis: Examining Kaizen in Greater Detail:
Kaizen isn't just about incremental improvements; it's a deeply ingrained cultural philosophy. It emphasizes the collective responsibility of all employees for continuous improvement. Toyota's success in fostering a culture of kaizen demonstrates the powerful impact of employee empowerment and the importance of a systematic approach to continuous improvement.
FAQ Section:
- What is the Toyota Production System (TPS)? TPS is a lean manufacturing methodology that focuses on eliminating waste, maximizing efficiency, and empowering employees to improve processes.
- How does Kaizen work at Toyota? Kaizen encourages every employee to suggest improvements, fostering a culture of continuous improvement. Suggestions are systematically reviewed and implemented.
- Is Toyota's bureaucracy inflexible? While Toyota has a hierarchical structure, it also empowers employees to contribute to decision-making and process improvement, mitigating rigidity.
Practical Tips: Learning from Toyota's Success:
- Embrace Lean Principles: Implement lean manufacturing principles to eliminate waste and improve efficiency.
- Foster a Culture of Kaizen: Encourage employee suggestions and create a systematic process for implementing improvements.
- Standardize Processes: Develop standardized procedures to ensure consistency and reduce variability.
- Invest in Training: Provide employees with the training and tools they need to contribute to continuous improvement.
Final Conclusion: A Model of Operational Excellence:
Toyota's organizational structure isn't just a bureaucratic machine; it's a finely tuned system that drives innovation, ensures quality, and underpins its global success. By carefully studying its structure and its effective implementation of lean principles, other organizations can learn valuable lessons about achieving operational excellence. Toyota's model stands as a testament to the power of a well-structured bureaucracy when combined with a culture of continuous improvement and employee empowerment.
Latest Posts
Latest Posts
-
Bond Buyer 20 Definition
Apr 19, 2025
-
What Is A Home Equity Investment
Apr 19, 2025
-
Bond Bank Definition
Apr 19, 2025
-
Bond Attorney Definition
Apr 19, 2025
-
How To Use Equity To Buy Investment Property
Apr 19, 2025
Related Post
Thank you for visiting our website which covers about What Bureau Does Toyota Pull . We hope the information provided has been useful to you. Feel free to contact us if you have any questions or need further assistance. See you next time and don't miss to bookmark.