What Are Workplace Controls
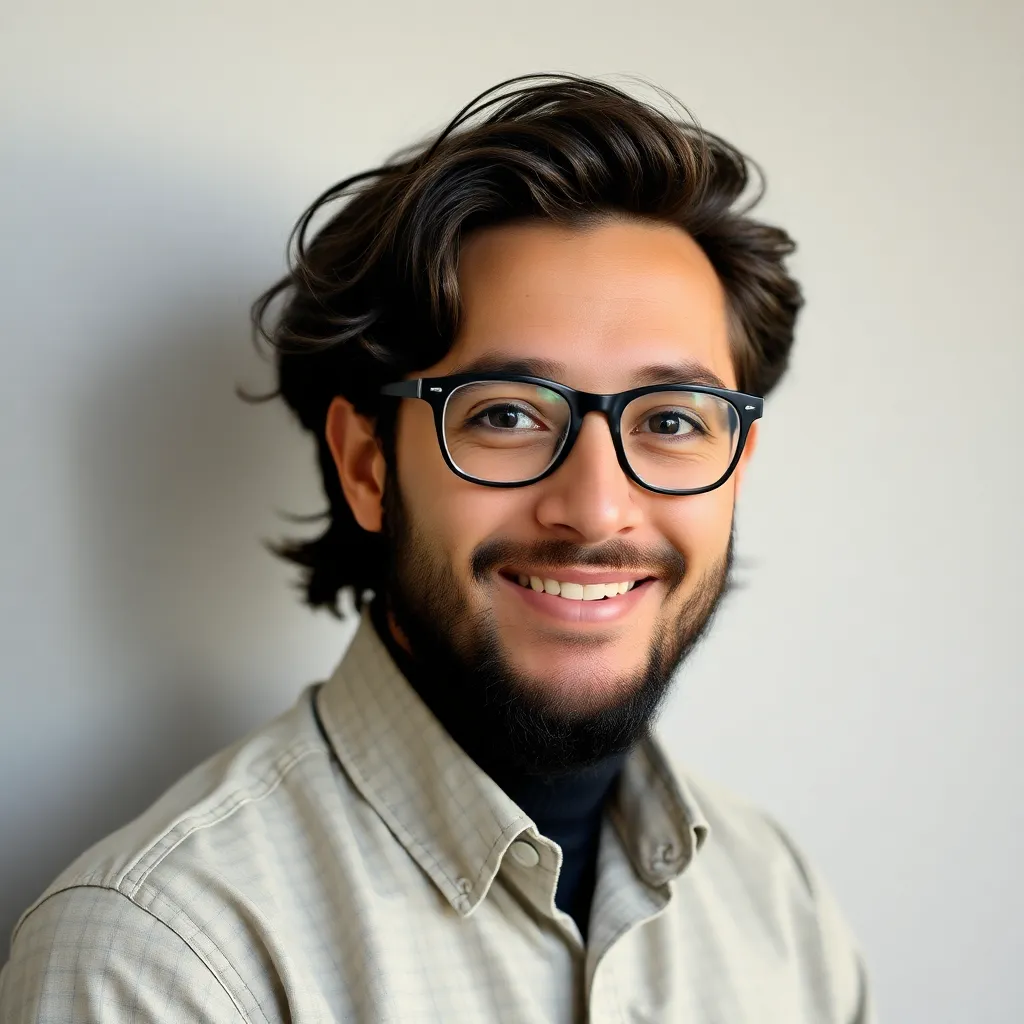
adminse
Apr 01, 2025 · 8 min read
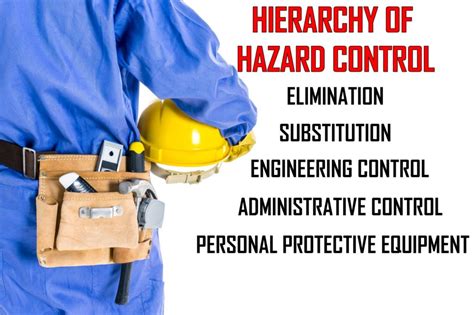
Table of Contents
Mastering Workplace Controls: A Comprehensive Guide to Safety and Productivity
What if the future of work depends on effectively implementing workplace controls? A robust control system is no longer a suggestion but a cornerstone of a safe, productive, and legally compliant workplace.
Editor’s Note: This article on workplace controls has been published today, providing readers with the latest information and best practices for creating a safe and efficient work environment.
Why Workplace Controls Matter:
Workplace controls are the cornerstone of any effective occupational safety and health (OSH) program. They are the systematic actions and measures implemented to eliminate or minimize hazards in the workplace, thereby protecting workers from injury, illness, and death. The benefits extend far beyond safety, encompassing increased productivity, improved employee morale, reduced absenteeism, lower insurance premiums, and enhanced legal compliance. Ignoring workplace controls can lead to significant financial penalties, legal repercussions, reputational damage, and, most tragically, preventable workplace incidents.
Overview: What This Article Covers:
This article will delve into the core aspects of workplace controls, exploring their different types, implementation strategies, and the critical role they play in maintaining a healthy and productive work environment. Readers will gain a comprehensive understanding of hazard identification, control selection, and the ongoing monitoring and evaluation necessary for a successful OSH program. We will also examine specific examples and case studies to illustrate practical applications across diverse industries.
The Research and Effort Behind the Insights:
This article is the result of extensive research, drawing upon established OSH standards, industry best practices, case studies, and relevant legal frameworks. Information has been gathered from reputable sources, including the Occupational Safety and Health Administration (OSHA), the National Institute for Occupational Safety and Health (NIOSH), and other leading authorities in occupational safety.
Key Takeaways:
- Definition and Core Concepts: A clear understanding of workplace controls and their hierarchy.
- Types of Controls: A detailed exploration of engineering, administrative, and personal protective equipment (PPE) controls.
- Hazard Identification and Risk Assessment: Methods for identifying and assessing workplace hazards effectively.
- Implementing Controls: A step-by-step approach to implementing and maintaining control measures.
- Monitoring and Evaluation: Continuous assessment and improvement of the control program.
- Legal and Regulatory Compliance: Understanding the legal obligations related to workplace controls.
- Specific Examples and Case Studies: Practical applications of workplace controls across various industries.
Smooth Transition to the Core Discussion:
With a clear understanding of the importance of workplace controls, let's delve deeper into their core components, exploring their practical applications and the strategies for successful implementation.
Exploring the Key Aspects of Workplace Controls:
1. Definition and Core Concepts:
Workplace controls are actions and measures taken to prevent or reduce exposure to workplace hazards. The central concept is the hierarchy of controls, a prioritized approach that emphasizes the most effective methods first. This hierarchy typically ranks controls from most effective to least effective as follows:
- Elimination: The most effective control method, involving completely removing the hazard from the workplace. For example, replacing a hazardous chemical with a safer alternative.
- Substitution: Replacing a hazardous substance, process, or piece of equipment with a less hazardous one. For instance, using water-based paints instead of oil-based paints.
- Engineering Controls: Implementing physical changes to the workplace to control hazards at the source. Examples include machine guarding, ventilation systems, and improved lighting.
- Administrative Controls: Modifying work practices, schedules, or procedures to reduce hazard exposure. Examples include job rotation, training programs, and limiting exposure time.
- Personal Protective Equipment (PPE): Providing workers with equipment to protect them from hazards when other controls are insufficient. This is considered the last line of defense and should be used in conjunction with other control measures. Examples include safety glasses, gloves, respirators, and hard hats.
2. Hazard Identification and Risk Assessment:
Before implementing any control measures, a thorough hazard identification and risk assessment is crucial. This process involves systematically identifying potential hazards in the workplace, analyzing the likelihood and severity of harm, and prioritizing control measures based on the identified risks. Common methods include:
- Workplace inspections: Regularly inspecting the workplace to identify potential hazards.
- Job hazard analyses (JHAs): Breaking down job tasks to identify specific hazards and control measures.
- Incident investigations: Analyzing past incidents to identify underlying causes and prevent future occurrences.
- Near-miss reporting: Encouraging employees to report near-miss incidents to identify potential hazards before they cause harm.
3. Implementing Controls:
Implementing controls requires a systematic approach, including:
- Selecting appropriate controls: Choosing controls based on the hierarchy of controls and the specific hazard.
- Designing and installing controls: Ensuring that controls are properly designed, installed, and maintained.
- Training employees: Providing employees with training on the use and maintenance of controls.
- Developing procedures: Establishing clear procedures for using and maintaining controls.
- Monitoring and evaluation: Regularly monitoring and evaluating the effectiveness of controls.
4. Monitoring and Evaluation:
Continuous monitoring and evaluation are crucial to ensure the effectiveness of workplace controls. This includes:
- Regular inspections: Regularly inspecting the workplace to ensure controls are in place and functioning correctly.
- Performance monitoring: Monitoring the performance of controls to identify any deficiencies.
- Employee feedback: Seeking feedback from employees about the effectiveness of controls.
- Record keeping: Maintaining accurate records of inspections, performance monitoring, and employee feedback.
5. Legal and Regulatory Compliance:
Employers have a legal and ethical obligation to provide a safe and healthy work environment. Compliance with relevant OSH regulations and standards is crucial, and this often includes specific requirements for workplace controls. Failure to comply can result in significant penalties, including fines and legal action.
Exploring the Connection Between Training and Workplace Controls:
The relationship between training and workplace controls is paramount. Effective workplace controls are rendered useless without proper training. Training ensures that employees understand the hazards they face, the controls in place to mitigate those hazards, and how to use those controls safely and effectively.
Key Factors to Consider:
-
Roles and Real-World Examples: Training programs should be tailored to specific roles and responsibilities, with practical examples and scenarios to reinforce learning. For instance, training for machine operators will focus on machine guarding and lockout/tagout procedures, while training for laboratory personnel will emphasize chemical handling and safety protocols.
-
Risks and Mitigations: Training should identify potential risks associated with failing to use controls correctly and explain mitigation strategies. This could include explaining the consequences of bypassing safety mechanisms or not using PPE properly.
-
Impact and Implications: Training should highlight the impact of proper control usage on individual safety, team productivity, and overall company performance. This demonstrates the direct link between safety and operational success.
Conclusion: Reinforcing the Connection:
The interplay between training and workplace controls is undeniable. Effective training empowers employees to utilize controls correctly, maximizing their protective effect and building a strong safety culture. Neglecting training renders even the most sophisticated controls ineffective, increasing the risk of accidents and injuries.
Further Analysis: Examining Training Methods in Greater Detail:
Effective training utilizes diverse methods to cater to different learning styles. This can include classroom lectures, hands-on demonstrations, simulations, online modules, and regular refresher courses. Regular assessments and feedback mechanisms ensure that employees retain the knowledge and skills necessary to work safely.
FAQ Section: Answering Common Questions About Workplace Controls:
-
What is the difference between engineering and administrative controls? Engineering controls are physical modifications to the workplace, while administrative controls involve changes to work practices or procedures.
-
How often should workplace controls be inspected? The frequency of inspections depends on the hazard and the control in place. High-risk areas may require daily inspections, while lower-risk areas might only require monthly or quarterly checks.
-
What are the legal consequences of not implementing appropriate workplace controls? Failure to implement appropriate controls can result in fines, legal action, and reputational damage. Severe violations can lead to business closures.
-
How can I involve employees in the development and implementation of workplace controls? Employee involvement is crucial. Utilize safety committees, toolbox talks, and suggestion boxes to solicit feedback and incorporate employee insights into the process.
Practical Tips: Maximizing the Benefits of Workplace Controls:
-
Conduct regular hazard identification and risk assessments: Proactively identify and address potential hazards before they cause incidents.
-
Prioritize controls according to the hierarchy of controls: Focus on elimination and substitution whenever possible.
-
Implement a comprehensive training program: Ensure that employees understand and can use controls effectively.
-
Establish clear procedures for using and maintaining controls: Document procedures and provide employees with access to them.
-
Monitor and evaluate controls regularly: Ensure that controls remain effective and address any deficiencies promptly.
-
Involve employees in the process: Encourage feedback and participation to foster a strong safety culture.
Final Conclusion: Wrapping Up with Lasting Insights:
Workplace controls are not merely a regulatory requirement; they are an investment in a safer, healthier, and more productive work environment. By implementing a comprehensive control program and fostering a strong safety culture, organizations can significantly reduce the risk of workplace incidents, improve employee morale, enhance productivity, and ensure compliance with all relevant regulations. The commitment to workplace controls is a commitment to a future where work is safe, fulfilling, and sustainable.
Latest Posts
Latest Posts
-
When Does Fpl Return
Apr 03, 2025
-
Tag Renewal Fee Florida
Apr 03, 2025
-
Late Fee For Registration Renewal Florida
Apr 03, 2025
-
Is There A Grace Period For Expired Tags In Florida
Apr 03, 2025
-
Late Fee For Tag Renewal
Apr 03, 2025
Related Post
Thank you for visiting our website which covers about What Are Workplace Controls . We hope the information provided has been useful to you. Feel free to contact us if you have any questions or need further assistance. See you next time and don't miss to bookmark.