Reserve Maintenance Period Definition
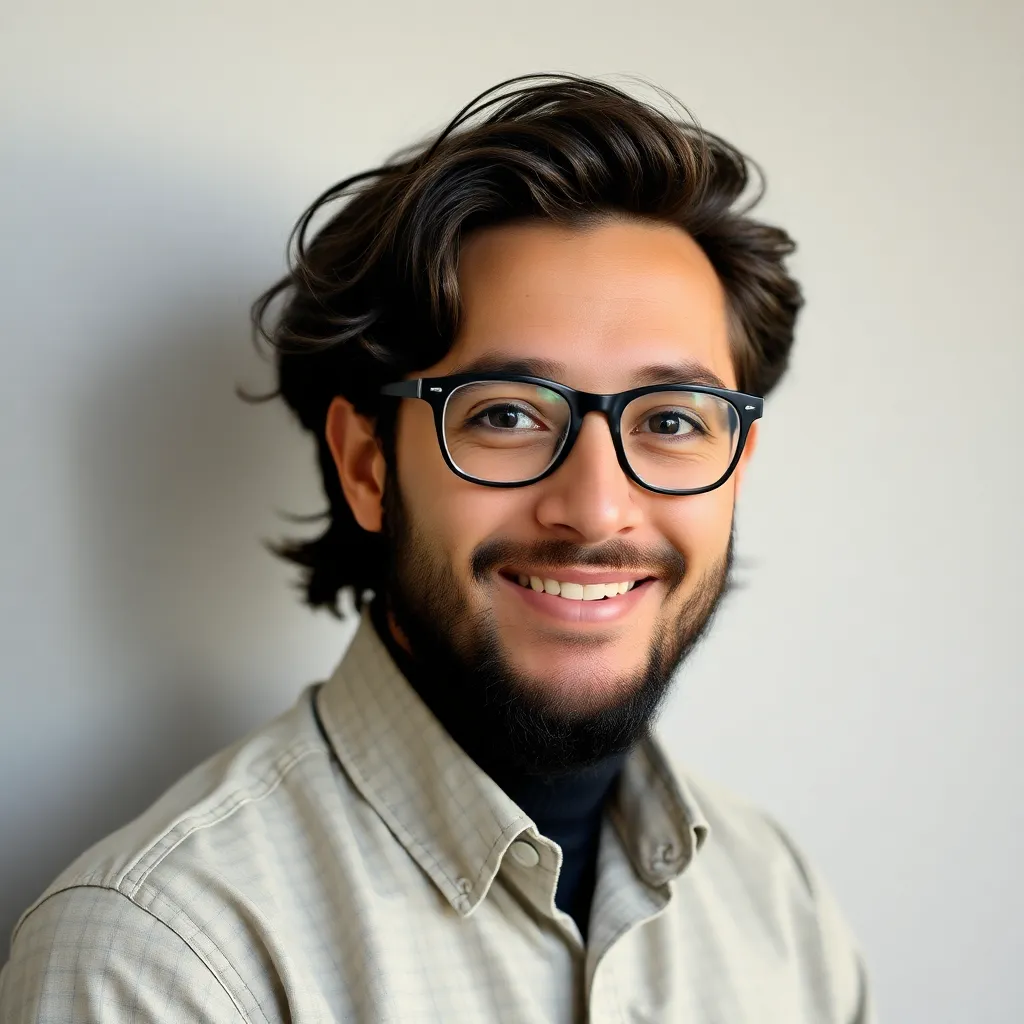
adminse
Apr 28, 2025 · 8 min read

Table of Contents
What if the optimal performance of your critical systems hinges on understanding Reserve Maintenance Periods?
Proactive reserve maintenance planning is no longer a luxury; it's a cornerstone of operational excellence and risk mitigation.
Editor’s Note: This article on Reserve Maintenance Period definitions and best practices has been published today, offering readers up-to-date insights into this crucial aspect of operational management. This comprehensive guide is designed for facility managers, IT professionals, and anyone responsible for maintaining critical systems and infrastructure.
Why Reserve Maintenance Periods Matter: Relevance, Practical Applications, and Industry Significance
Reserve Maintenance Periods (RMPs), also sometimes referred to as planned maintenance windows, scheduled downtime, or planned outages, are dedicated timeframes specifically allocated for performing preventative and corrective maintenance on critical systems or equipment. The importance of effective RMPs cannot be overstated. They are fundamental to extending the lifespan of assets, preventing catastrophic failures, ensuring regulatory compliance, minimizing disruptions to operations, and ultimately, saving organizations significant time and money. Across various industries – from manufacturing and healthcare to data centers and transportation – well-defined and executed RMPs are a critical component of successful operational strategies. Their relevance spans across various departments, requiring collaboration between engineering, IT, operations, and even customer service teams.
Overview: What This Article Covers
This article provides a comprehensive understanding of Reserve Maintenance Periods, encompassing their definition, planning, execution, and optimization. We will explore various methodologies, best practices, and potential challenges, offering actionable insights for effective RMP implementation. Readers will gain a clear understanding of the benefits, potential risks, and strategies for maximizing the efficiency and minimizing the disruption associated with scheduled downtime.
The Research and Effort Behind the Insights
This article is the result of extensive research, drawing upon industry best practices, technical documentation, case studies, and regulatory guidelines. The information presented is supported by evidence-based analysis to ensure accuracy and provide readers with reliable and trustworthy information. The structured approach, encompassing different aspects of RMP management, aims to provide practical guidance and actionable insights.
Key Takeaways: Summarize the Most Essential Insights
- Definition and Core Concepts: A clear explanation of RMPs, their purpose, and key characteristics.
- Planning and Scheduling: Strategies for effective RMP planning, including risk assessment, resource allocation, and communication.
- Execution and Monitoring: Best practices for efficient execution and real-time monitoring of maintenance activities.
- Optimization and Continuous Improvement: Methods for optimizing RMP schedules and minimizing downtime through data analysis and feedback loops.
- Addressing Challenges: Common challenges encountered during RMPs and strategies for mitigation.
- Compliance and Regulatory Aspects: The role of RMPs in meeting regulatory requirements and industry standards.
Smooth Transition to the Core Discussion
With a clear understanding of why RMPs are critical for operational efficiency and risk management, let's delve deeper into the key aspects of planning, executing, and optimizing these crucial maintenance periods.
Exploring the Key Aspects of Reserve Maintenance Periods
Definition and Core Concepts: A Reserve Maintenance Period (RMP) is a pre-planned and scheduled period of inactivity for a system or piece of equipment, allocated specifically for maintenance activities. This downtime is intentionally introduced to perform preventative maintenance (PM), corrective maintenance (CM), or upgrades. The goal is to minimize unexpected downtime and maximize the operational lifespan and reliability of the assets. Crucially, RMPs are distinct from unplanned downtime caused by unexpected failures. They are a proactive measure, allowing for scheduled interventions rather than reactive repairs.
Planning and Scheduling: Effective RMP planning is paramount. This begins with a comprehensive risk assessment identifying critical systems and the potential impact of their failure. A detailed maintenance schedule must be developed, considering factors like the frequency of maintenance, the duration of each task, the availability of resources (personnel, tools, parts), and the impact on operational continuity. This schedule needs to be carefully coordinated with other operational activities, taking into account factors such as peak demand periods, production cycles, and customer service requirements. Sophisticated scheduling software can be invaluable in managing complex RMP schedules.
Execution and Monitoring: During the RMP, strict adherence to the planned schedule is critical. Real-time monitoring of progress is crucial to identify and address any deviations promptly. Effective communication between maintenance personnel and operational teams ensures efficient coordination and minimizes disruptions. Using checklists, work orders, and reporting systems ensures accountability and allows for thorough documentation of all work performed. This documentation is crucial for tracking maintenance history, optimizing future RMPs, and complying with regulatory requirements.
Optimization and Continuous Improvement: The goal is not merely to conduct maintenance but to optimize the RMP process continually. Data analysis of past maintenance activities, including downtime duration, resource utilization, and the effectiveness of different maintenance strategies, can inform future planning. Regular reviews of the RMP schedule and procedures should be conducted to identify areas for improvement and enhance efficiency. Feedback from maintenance personnel and operational teams is invaluable in refining the process.
Addressing Challenges: Several challenges can hinder the effectiveness of RMPs. Resource constraints, including limited personnel or budget, can delay or compromise maintenance activities. Inadequate planning or unforeseen complications during maintenance can lead to extended downtime. Difficulties in coordinating maintenance across multiple systems or teams can also create significant obstacles. Effective risk management and mitigation strategies, including contingency planning and proactive communication, are vital for addressing these challenges.
Compliance and Regulatory Aspects: Many industries have strict regulations governing the maintenance of critical systems and equipment. Compliance with these regulations often requires a well-defined RMP process, detailed documentation, and regular audits. Failure to comply can result in significant penalties, operational disruptions, and reputational damage. A thorough understanding of applicable regulations and industry best practices is essential for ensuring compliance.
Exploring the Connection Between Risk Assessment and Reserve Maintenance Periods
The relationship between risk assessment and RMPs is fundamentally intertwined. A robust risk assessment is the cornerstone of effective RMP planning. It identifies critical systems, the potential consequences of their failure, and the likelihood of those failures occurring. This information informs the prioritization of maintenance tasks, the allocation of resources, and the scheduling of RMPs. Without a thorough risk assessment, the RMP process risks being inefficient, ineffective, and potentially dangerous.
Key Factors to Consider:
-
Roles and Real-World Examples: Risk assessment methodologies, such as Failure Mode and Effects Analysis (FMEA) and Fault Tree Analysis (FTA), are used to identify potential failures and their consequences. For example, in a data center, a risk assessment might identify the risk of server failure, the potential impact on business operations, and the likelihood of this failure occurring. This information would then be used to schedule RMPs for server maintenance, ensuring preventative measures are taken to minimize the risk of downtime.
-
Risks and Mitigations: A critical aspect of risk assessment is identifying potential risks associated with RMPs themselves. For example, poorly planned maintenance could lead to extended downtime or even damage to equipment. Mitigation strategies include thorough planning, rigorous testing, and robust communication protocols.
-
Impact and Implications: The impact of an effective RMP program can be significant. It can reduce the frequency and severity of unexpected downtime, improve operational efficiency, enhance safety, and strengthen regulatory compliance. Conversely, a poorly managed RMP program can lead to increased downtime, equipment damage, safety risks, and regulatory non-compliance.
Conclusion: Reinforcing the Connection
The interplay between risk assessment and RMPs underscores the importance of proactive planning and meticulous execution. By carefully assessing risks and incorporating those findings into the RMP process, organizations can mitigate potential problems, optimize maintenance schedules, and achieve significant operational improvements.
Further Analysis: Examining Risk Assessment Methodologies in Greater Detail
Several methodologies are employed for effective risk assessment. Failure Mode and Effects Analysis (FMEA) is a systematic process for identifying potential failure modes, their causes, and their effects on the system. Fault Tree Analysis (FTA) is a top-down approach that works backward from an undesired event (e.g., system failure) to identify the root causes. Both FMEA and FTA provide valuable input for developing effective RMPs.
FAQ Section: Answering Common Questions About Reserve Maintenance Periods
-
What is a Reserve Maintenance Period? A Reserve Maintenance Period (RMP) is a scheduled period of downtime allocated specifically for performing preventative and corrective maintenance on critical systems or equipment.
-
Why are RMPs important? RMPs are crucial for extending the lifespan of assets, preventing catastrophic failures, ensuring regulatory compliance, minimizing disruptions to operations, and ultimately, saving organizations significant time and money.
-
How are RMPs planned and scheduled? Effective RMP planning involves a comprehensive risk assessment, the development of a detailed maintenance schedule, coordination with operational activities, and resource allocation.
-
What are the challenges associated with RMPs? Challenges include resource constraints, inadequate planning, unforeseen complications during maintenance, and difficulties in coordinating maintenance across multiple systems or teams.
-
How can RMPs be optimized? Continuous improvement can be achieved through data analysis, regular reviews of the RMP schedule and procedures, and feedback from maintenance personnel and operational teams.
Practical Tips: Maximizing the Benefits of Reserve Maintenance Periods
- Conduct Thorough Risk Assessments: Identify critical systems and potential failure modes before developing the RMP schedule.
- Develop a Detailed Maintenance Schedule: Include all necessary tasks, their durations, and required resources.
- Communicate Effectively: Keep all stakeholders informed of planned downtime and any potential disruptions.
- Use Maintenance Management Software: Utilize software to streamline scheduling, tracking, and reporting.
- Monitor and Evaluate Performance: Track key metrics to identify areas for improvement and optimize future RMPs.
Final Conclusion: Wrapping Up with Lasting Insights
Reserve Maintenance Periods represent a critical component of operational excellence and risk management. By embracing proactive planning, thorough risk assessment, and continuous improvement, organizations can optimize their RMP processes, minimizing downtime, maximizing asset lifespan, and ultimately achieving significant cost savings and improved operational reliability. The proactive approach embodied in RMPs shifts the focus from reactive firefighting to preventative care, leading to more resilient and efficient operations. Investing in a well-defined and effectively executed RMP program is not an expense; it's a strategic investment in operational longevity and success.
Latest Posts
Latest Posts
-
Retail Note Definition
Apr 28, 2025
-
Retail Investor Definition What They Do And Market Impact
Apr 28, 2025
-
When Do I Need To Recertify Student Loans
Apr 28, 2025
-
How Long Does Student Loans Stay On Credit Report
Apr 28, 2025
-
Retail Inventory Method Definition Calculation And Example
Apr 28, 2025
Related Post
Thank you for visiting our website which covers about Reserve Maintenance Period Definition . We hope the information provided has been useful to you. Feel free to contact us if you have any questions or need further assistance. See you next time and don't miss to bookmark.