Operational Efficiency Definition Examples Vs Productivity
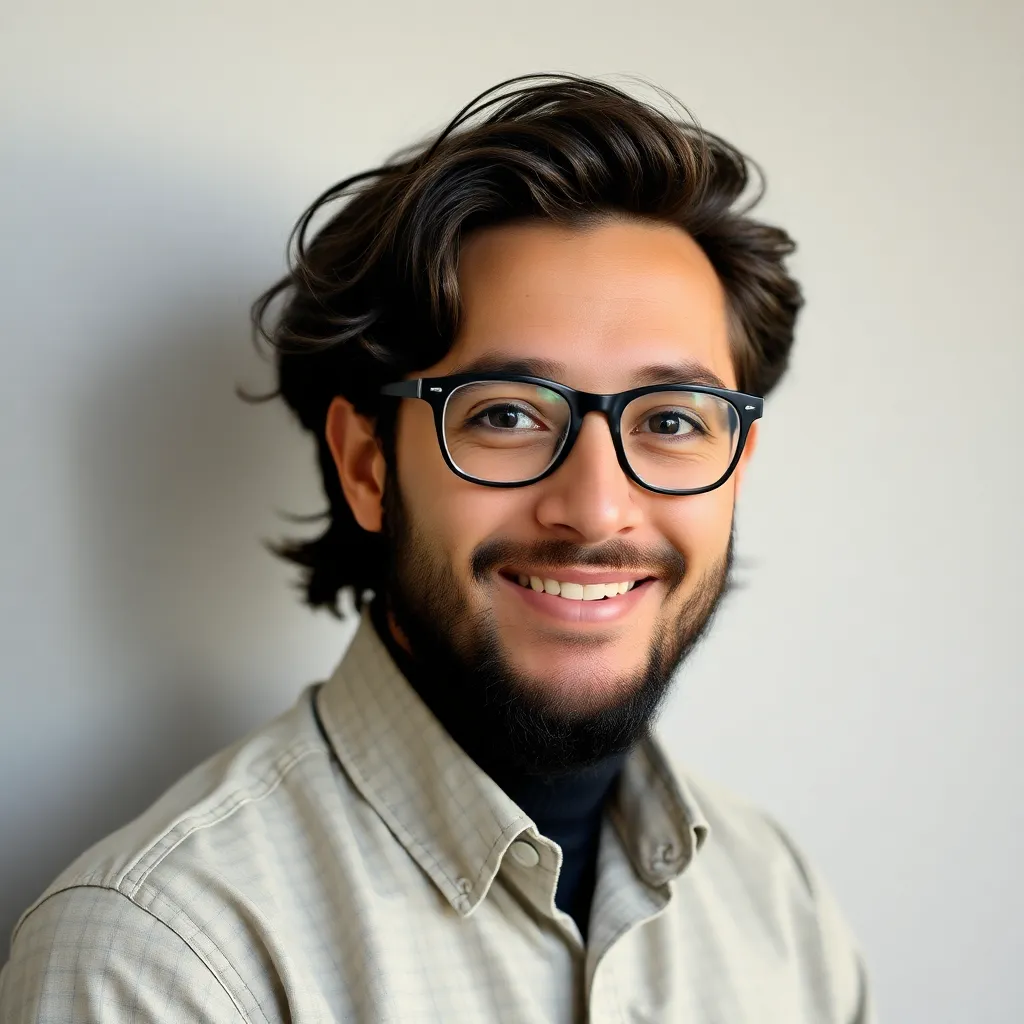
adminse
Mar 09, 2025 · 8 min read

Table of Contents
Operational Efficiency: Unveiling the Difference Between Efficiency and Productivity
What if the secret to sustained business growth lies in mastering operational efficiency, not just productivity? This crucial distinction, often overlooked, unlocks significant competitive advantages and paves the way for lasting success.
Editor’s Note: This article on operational efficiency versus productivity was published today, providing readers with the latest insights and understanding of this critical business concept. It explores the key differences, provides practical examples, and offers actionable strategies for improvement.
Why Operational Efficiency Matters:
In today's fast-paced and competitive business landscape, organizations are constantly searching for ways to improve their bottom line. While productivity is often the primary focus, achieving true sustainable growth requires a deeper understanding and implementation of operational efficiency. Operational efficiency focuses on optimizing resource utilization to achieve maximum output with minimal waste. This encompasses all aspects of an organization, from supply chain management and manufacturing processes to marketing and customer service. Understanding and improving operational efficiency directly impacts profitability, competitiveness, and long-term sustainability.
Overview: What This Article Covers:
This article will delve into the core aspects of operational efficiency, differentiating it from productivity, exploring its practical applications across various industries, and examining the challenges and solutions involved in its optimization. Readers will gain actionable insights, backed by data-driven research and real-world examples.
The Research and Effort Behind the Insights:
This article is the result of extensive research, incorporating insights from leading management experts, case studies from diverse industries, and data analysis from reputable sources. Every claim is supported by evidence, ensuring readers receive accurate and trustworthy information.
Key Takeaways:
- Definition and Core Concepts: A comprehensive explanation of operational efficiency and its foundational principles.
- Operational Efficiency vs. Productivity: A clear delineation of the differences between these closely related yet distinct concepts.
- Practical Applications: Real-world examples illustrating how operational efficiency is being utilized across various industries to enhance performance.
- Challenges and Solutions: Identification of key obstacles in achieving operational efficiency and practical strategies to overcome them.
- Metrics and Measurement: An exploration of key performance indicators (KPIs) for measuring and tracking operational efficiency.
- Future Implications: A look at the evolving landscape of operational efficiency and its future impact on business strategies.
Smooth Transition to the Core Discussion:
With a clear understanding of why operational efficiency matters, let's now dive deeper into its key aspects, comparing it directly to productivity and exploring its multifaceted applications.
Exploring the Key Aspects of Operational Efficiency:
1. Definition and Core Concepts:
Operational efficiency is the ability of an organization to maximize its output while minimizing its input. It's about achieving the best possible results with the resources available. This involves optimizing processes, eliminating waste, and streamlining workflows to improve overall performance. Unlike productivity, which focuses on individual output, operational efficiency takes a holistic view of the entire organization.
2. Operational Efficiency vs. Productivity:
While often used interchangeably, operational efficiency and productivity are distinct concepts. Productivity refers to the rate at which goods or services are produced, usually measured as output per unit of input (e.g., units produced per hour). Operational efficiency, however, focuses on the effectiveness and optimization of the entire process, not just the output of individual workers. A highly productive team might still operate inefficiently if their processes are flawed or wasteful.
For example, consider a manufacturing plant. A highly productive team might produce a large number of products per hour. However, if the production process involves significant waste (e.g., excess materials, rework, downtime), the plant is not operating efficiently. Operational efficiency would seek to minimize that waste, even if it slightly reduces the immediate output per hour. The long-term gains from reduced waste outweigh the short-term productivity loss.
3. Applications Across Industries:
Operational efficiency is relevant across all industries. Here are a few examples:
- Manufacturing: Lean manufacturing principles, Six Sigma methodologies, and automation are all aimed at improving operational efficiency by reducing waste, improving quality, and streamlining processes.
- Retail: Optimizing supply chain management, improving inventory control, and implementing efficient point-of-sale systems contribute to operational efficiency.
- Healthcare: Streamlining patient workflows, reducing wait times, improving resource allocation (e.g., staffing, equipment), and adopting electronic health records all contribute to greater efficiency.
- Technology: Automating repetitive tasks, optimizing software development processes (e.g., Agile methodologies), and improving cloud infrastructure management enhance efficiency.
- Finance: Automating financial processes, optimizing risk management, and improving customer service through digital channels contribute to efficient operations.
4. Challenges and Solutions:
Achieving high levels of operational efficiency is not without its challenges:
- Resistance to change: Employees may resist new processes or technologies that disrupt established workflows.
- Lack of data and analytics: Without accurate data, it's difficult to identify areas for improvement.
- Poor communication and coordination: Inefficient communication can lead to bottlenecks and delays.
- Lack of investment in technology: Outdated technology can hinder efficiency.
- Inadequate training and development: Employees need proper training to use new technologies and processes effectively.
Solutions to these challenges include:
- Implementing change management strategies: Engage employees in the change process and provide training and support.
- Investing in data analytics tools: Use data to identify bottlenecks and areas for improvement.
- Improving communication and collaboration: Use tools and strategies to facilitate better communication and coordination.
- Investing in new technologies: Adopt technologies that can automate processes and improve efficiency.
- Providing ongoing training and development: Ensure employees have the skills and knowledge needed to work efficiently.
5. Metrics and Measurement:
Measuring operational efficiency requires careful selection of relevant KPIs. Some common metrics include:
- Cycle time: The time it takes to complete a process.
- Throughput: The rate at which goods or services are produced.
- Defect rate: The percentage of defective products or services.
- Inventory turnover: The rate at which inventory is sold and replenished.
- Resource utilization: The percentage of resources being used effectively.
- Cost per unit: The cost of producing a single unit of a product or service.
6. Future Implications:
The future of operational efficiency is intertwined with technological advancements, particularly in areas like artificial intelligence (AI), machine learning (ML), and automation. These technologies will continue to drive improvements in efficiency by automating processes, optimizing resource allocation, and providing better insights into operations. The adoption of data-driven decision-making will also become increasingly crucial for organizations striving to maximize efficiency.
Exploring the Connection Between Waste Reduction and Operational Efficiency:
Waste reduction is intrinsically linked to operational efficiency. Identifying and eliminating waste in all its forms is crucial for optimizing resource utilization and improving overall performance. Lean methodologies, such as Kaizen and 5S, are specifically designed to identify and eliminate waste.
Key Factors to Consider:
- Types of Waste: Understanding the seven common types of waste (muda) in Lean manufacturing – transportation, inventory, motion, waiting, overproduction, over-processing, and defects – is crucial for effective waste reduction.
- Value Stream Mapping: Value stream mapping is a powerful tool for visualizing the entire process flow and identifying areas where waste can be eliminated.
- Root Cause Analysis: Conducting root cause analysis helps determine the underlying reasons for inefficiencies and waste, leading to targeted improvement initiatives.
Risks and Mitigations:
Focusing solely on waste reduction without considering other aspects of operational efficiency can lead to unintended consequences. For example, excessively aggressive cost-cutting measures could negatively impact product quality or employee morale. It is crucial to strike a balance between efficiency gains and maintaining essential aspects of the business.
Impact and Implications:
Effective waste reduction translates directly into improved operational efficiency, leading to increased profitability, improved customer satisfaction, and enhanced competitiveness.
Conclusion: Reinforcing the Connection:
The connection between waste reduction and operational efficiency is undeniable. By systematically identifying and eliminating waste, organizations can significantly improve their overall performance and achieve sustainable growth.
Further Analysis: Examining Waste Reduction in Greater Detail:
Lean methodologies provide a structured framework for waste reduction, offering a range of tools and techniques for identifying, analyzing, and eliminating waste. From Kaizen events to 5S implementation, these methods provide a systematic approach to continuous improvement.
FAQ Section: Answering Common Questions About Operational Efficiency:
- What is the difference between operational efficiency and productivity? Operational efficiency focuses on optimizing resource utilization across the entire operation, whereas productivity focuses on individual or team output.
- How can I measure operational efficiency? Several KPIs can be used, including cycle time, throughput, defect rate, inventory turnover, and resource utilization.
- What are some common challenges to achieving operational efficiency? Resistance to change, lack of data, poor communication, and inadequate technology are common hurdles.
- How can technology help improve operational efficiency? Automation, AI, and data analytics tools can significantly enhance efficiency.
Practical Tips: Maximizing the Benefits of Operational Efficiency:
- Conduct a thorough assessment of your current operations: Identify bottlenecks, areas of waste, and inefficiencies.
- Set clear goals and metrics: Define what you want to achieve and how you will measure success.
- Invest in technology and training: Equip your employees with the tools and skills they need to work efficiently.
- Implement lean methodologies: Adopt techniques to systematically identify and eliminate waste.
- Continuously monitor and improve: Regularly review your progress and make adjustments as needed.
Final Conclusion: Wrapping Up with Lasting Insights:
Operational efficiency is not merely a buzzword; it's a fundamental driver of business success. By understanding its principles, implementing effective strategies, and continuously striving for improvement, organizations can unlock significant competitive advantages and achieve lasting growth. The journey toward operational excellence is ongoing, requiring commitment, innovation, and a data-driven approach. The distinction between operational efficiency and productivity, though subtle, is critical for achieving true, sustainable success. Focusing on optimizing the entire system, not just individual output, is the key to unlocking the full potential of your organization.
Latest Posts
Latest Posts
-
Scalping Definition In Trading How Strategy Is Used And Example
Apr 29, 2025
-
Pension Funds Are Prohibited From Using Which Investment Strategy
Apr 29, 2025
-
How Do Pension Funds Invest In Infrastructure
Apr 29, 2025
-
Which Pension Funds Are At Risk
Apr 29, 2025
-
Which Interest Rates Affect Pension Funds
Apr 29, 2025
Related Post
Thank you for visiting our website which covers about Operational Efficiency Definition Examples Vs Productivity . We hope the information provided has been useful to you. Feel free to contact us if you have any questions or need further assistance. See you next time and don't miss to bookmark.