Lead Time Definition How It Works And Example
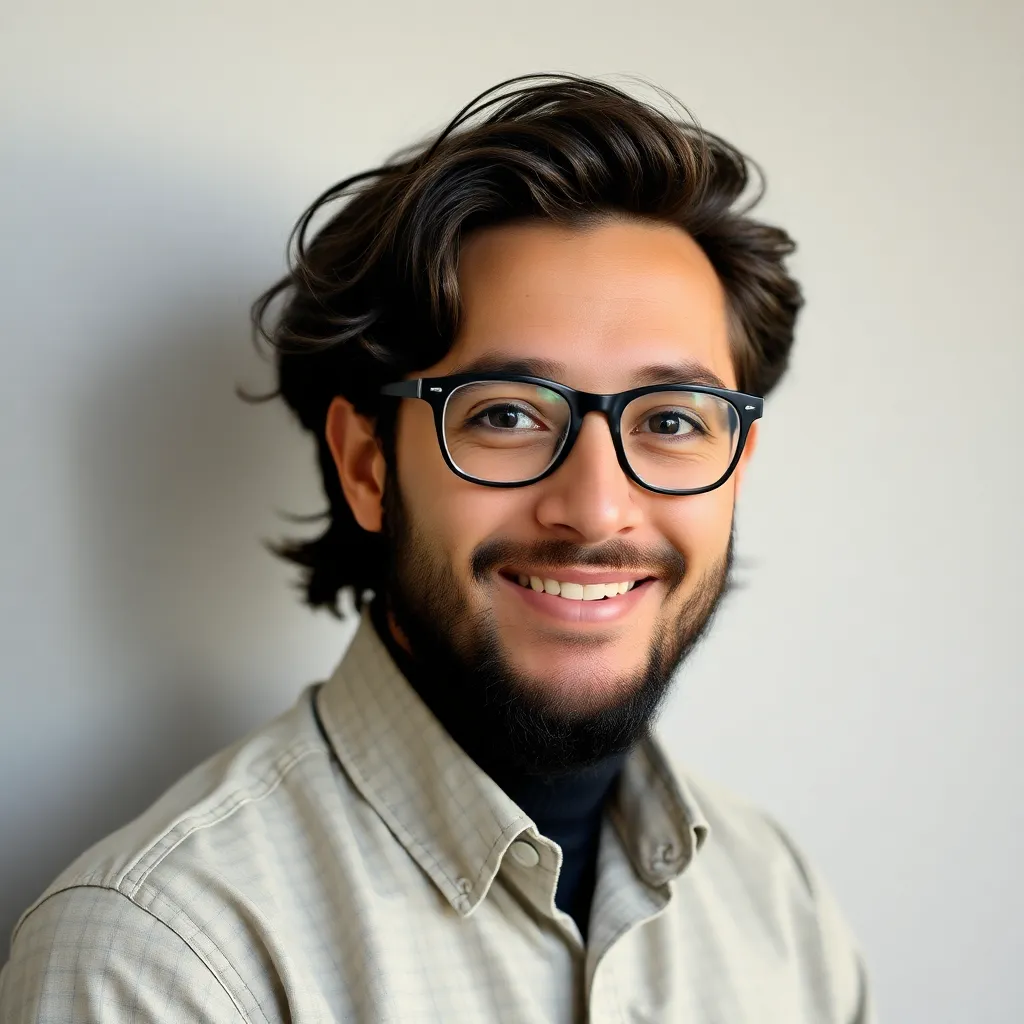
adminse
Apr 20, 2025 · 7 min read

Table of Contents
Understanding Lead Time: Definition, How It Works, and Real-World Examples
What if optimizing your lead time was the key to unlocking significant competitive advantage? Effective lead time management is no longer a nice-to-have; it's a fundamental requirement for success in today's fast-paced business environment.
Editor’s Note: This comprehensive guide to lead time was published today to provide readers with the latest insights and best practices in supply chain management and operational efficiency. This article covers the definition, functionality, calculation, and real-world application of lead time, empowering businesses to optimize their processes and gain a competitive edge.
Why Lead Time Matters:
Lead time, a seemingly simple concept, profoundly impacts a business's profitability, customer satisfaction, and overall competitiveness. It represents the total time required to fulfill an order, from the moment a customer places an order to the moment they receive the finished product or service. Minimizing lead time translates to faster delivery, increased responsiveness to market demands, reduced inventory costs, improved cash flow, and a stronger competitive position. Understanding and effectively managing lead time is crucial across diverse industries, from manufacturing and retail to software development and project management.
Overview: What This Article Covers:
This article provides a detailed exploration of lead time, encompassing its definition, various types, calculation methods, the factors influencing it, and strategies for its optimization. We will examine real-world examples across multiple industries, illustrating the practical applications and benefits of effective lead time management. The article also delves into the challenges associated with lead time reduction and offers practical solutions to overcome them.
The Research and Effort Behind the Insights:
This in-depth analysis draws upon extensive research, including academic literature on supply chain management, industry best practices, case studies from diverse organizations, and data from reputable sources. The information presented aims to provide readers with accurate, actionable insights backed by credible evidence.
Key Takeaways:
- Definition and Core Concepts: A clear understanding of lead time and its various components.
- Lead Time Calculation Methods: Practical approaches to accurately measure lead time.
- Factors Influencing Lead Time: Identifying key variables affecting lead time performance.
- Lead Time Optimization Strategies: Proven techniques to reduce and manage lead time effectively.
- Real-World Examples and Case Studies: Illustrative examples of successful lead time management.
- Challenges and Solutions: Addressing potential obstacles in lead time reduction initiatives.
Smooth Transition to the Core Discussion:
Having established the importance of lead time, let's delve into its core components and explore how it impacts different business functions.
Exploring the Key Aspects of Lead Time:
1. Definition and Core Concepts:
Lead time refers to the total elapsed time between initiating a process and its completion. In a manufacturing context, this encompasses the time from receiving a customer order to delivering the finished goods. In a service industry, it might represent the time between a service request and its fulfillment. Lead time is not just about production; it incorporates all stages, including order processing, procurement of raw materials, production, quality control, packaging, and shipping.
2. Types of Lead Time:
Several types of lead time exist, each representing a specific phase of the overall process:
- Order Lead Time: The time from receiving a customer order to shipping the finished product.
- Procurement Lead Time: The time required to obtain raw materials or components from suppliers.
- Manufacturing Lead Time: The time spent in the actual production process, encompassing all steps from raw materials to finished goods.
- Delivery Lead Time: The time taken to deliver the finished product to the customer.
- Total Lead Time: The sum of all lead times involved in the entire process.
3. Lead Time Calculation Methods:
Calculating lead time involves tracking the time spent in each stage of the process. Simple methods include using spreadsheets or dedicated software to record the start and end times of each activity. More sophisticated techniques involve statistical process control (SPC) to identify bottlenecks and optimize process flows. Accurate lead time data is crucial for effective management and improvement.
4. Factors Influencing Lead Time:
Numerous factors can influence lead time, including:
- Process Efficiency: Inefficient processes, bottlenecks, and delays significantly increase lead time.
- Supplier Reliability: Unreliable suppliers can cause delays in material procurement.
- Inventory Management: Inadequate inventory levels can halt production.
- Production Capacity: Insufficient production capacity can lead to longer lead times.
- Technology and Automation: Implementing advanced technology and automation can shorten lead times.
- Demand Fluctuations: Unexpected spikes in demand can stretch lead times.
- Quality Control: Rigorous quality control processes can increase lead time but improve product quality.
- Transportation and Logistics: Efficient transportation and logistics networks are crucial for timely delivery.
5. Lead Time Optimization Strategies:
Strategies for reducing lead time include:
- Process Mapping and Improvement: Identifying bottlenecks and streamlining processes.
- Inventory Optimization: Implementing Just-in-Time (JIT) inventory management techniques.
- Supplier Relationship Management (SRM): Developing strong relationships with reliable suppliers.
- Technology Implementation: Utilizing automation, ERP systems, and other technologies to improve efficiency.
- Capacity Planning: Ensuring sufficient production capacity to meet demand.
- Lean Manufacturing Principles: Adopting lean methodologies to eliminate waste and improve efficiency.
- Predictive Analytics: Using data to forecast demand and optimize resource allocation.
6. Impact on Innovation:
Reducing lead time allows businesses to respond more quickly to market changes and customer demands, fostering innovation by enabling faster product development cycles and quicker adaptation to evolving trends. A shorter lead time fosters a culture of agility and responsiveness, crucial for success in today's dynamic markets.
Closing Insights: Summarizing the Core Discussion:
Lead time optimization is not just about faster delivery; it’s about creating a more efficient, responsive, and profitable business. By implementing the strategies discussed, organizations can significantly improve their operational efficiency, enhance customer satisfaction, and gain a substantial competitive edge.
Exploring the Connection Between Inventory Management and Lead Time:
The relationship between inventory management and lead time is deeply intertwined. Excessive inventory can mask inefficiencies, leading to longer lead times and increased storage costs. Conversely, insufficient inventory can disrupt production and lengthen lead times. Effective inventory management is crucial for optimizing lead time.
Key Factors to Consider:
- Roles and Real-World Examples: Companies using Just-in-Time (JIT) inventory significantly reduce lead times by minimizing stock levels and coordinating production with demand. Conversely, businesses with large safety stock levels often experience longer lead times due to reduced production agility.
- Risks and Mitigations: Inadequate inventory management can lead to stockouts, halting production and delaying orders. Mitigation strategies include implementing robust forecasting techniques, maintaining buffer stock levels, and diversifying suppliers.
- Impact and Implications: Effective inventory management reduces lead times, improves cash flow, minimizes storage costs, and increases responsiveness to market changes. Poor inventory management results in increased lead times, higher inventory holding costs, and potential loss of sales due to stockouts.
Conclusion: Reinforcing the Connection:
The interplay between inventory management and lead time underscores the importance of integrated supply chain planning. By strategically managing inventory levels and optimizing procurement processes, organizations can achieve significant reductions in lead time, enhancing their overall efficiency and competitiveness.
Further Analysis: Examining Inventory Management in Greater Detail:
Effective inventory management involves a multifaceted approach, including demand forecasting, inventory control systems, and supplier collaboration. Advanced techniques like ABC analysis and Economic Order Quantity (EOQ) calculations can significantly optimize inventory levels and minimize lead times.
FAQ Section: Answering Common Questions About Lead Time:
- What is lead time? Lead time is the total time required to fulfill an order, from order placement to delivery.
- How is lead time calculated? Lead time is calculated by tracking the time spent in each stage of the process, from order placement to delivery.
- What factors influence lead time? Numerous factors, including process efficiency, supplier reliability, inventory management, and production capacity, influence lead time.
- How can lead time be reduced? Lead time can be reduced by streamlining processes, optimizing inventory levels, improving supplier relationships, and implementing advanced technologies.
- What are the benefits of reducing lead time? Reducing lead time leads to faster delivery, increased customer satisfaction, reduced costs, and improved competitiveness.
Practical Tips: Maximizing the Benefits of Lead Time Reduction:
- Map your processes: Identify bottlenecks and areas for improvement.
- Optimize your inventory: Implement Just-in-Time (JIT) or similar inventory management systems.
- Strengthen supplier relationships: Collaborate with reliable suppliers to ensure timely delivery of materials.
- Invest in technology: Utilize automation, ERP systems, and other technologies to streamline operations.
- Monitor and measure: Track lead time regularly to identify areas for improvement.
Final Conclusion: Wrapping Up with Lasting Insights:
Lead time is a critical factor influencing a business's overall success. By understanding its components, implementing effective management strategies, and fostering a culture of continuous improvement, organizations can transform lead time from a constraint into a strategic advantage, driving operational excellence and achieving sustainable growth. The insights provided in this article serve as a foundation for businesses to embark on their lead time optimization journey.
Latest Posts
Latest Posts
-
Sec Form 20fr12b Definition
Apr 29, 2025
-
What Is Sec Form 20 F Definition Requirements And Who Files
Apr 29, 2025
-
Sec Form 19b 4 Definition
Apr 29, 2025
-
Sec Form 18 K Definition
Apr 29, 2025
-
Sec Form 18 Definition
Apr 29, 2025
Related Post
Thank you for visiting our website which covers about Lead Time Definition How It Works And Example . We hope the information provided has been useful to you. Feel free to contact us if you have any questions or need further assistance. See you next time and don't miss to bookmark.