Double Gearing Definition
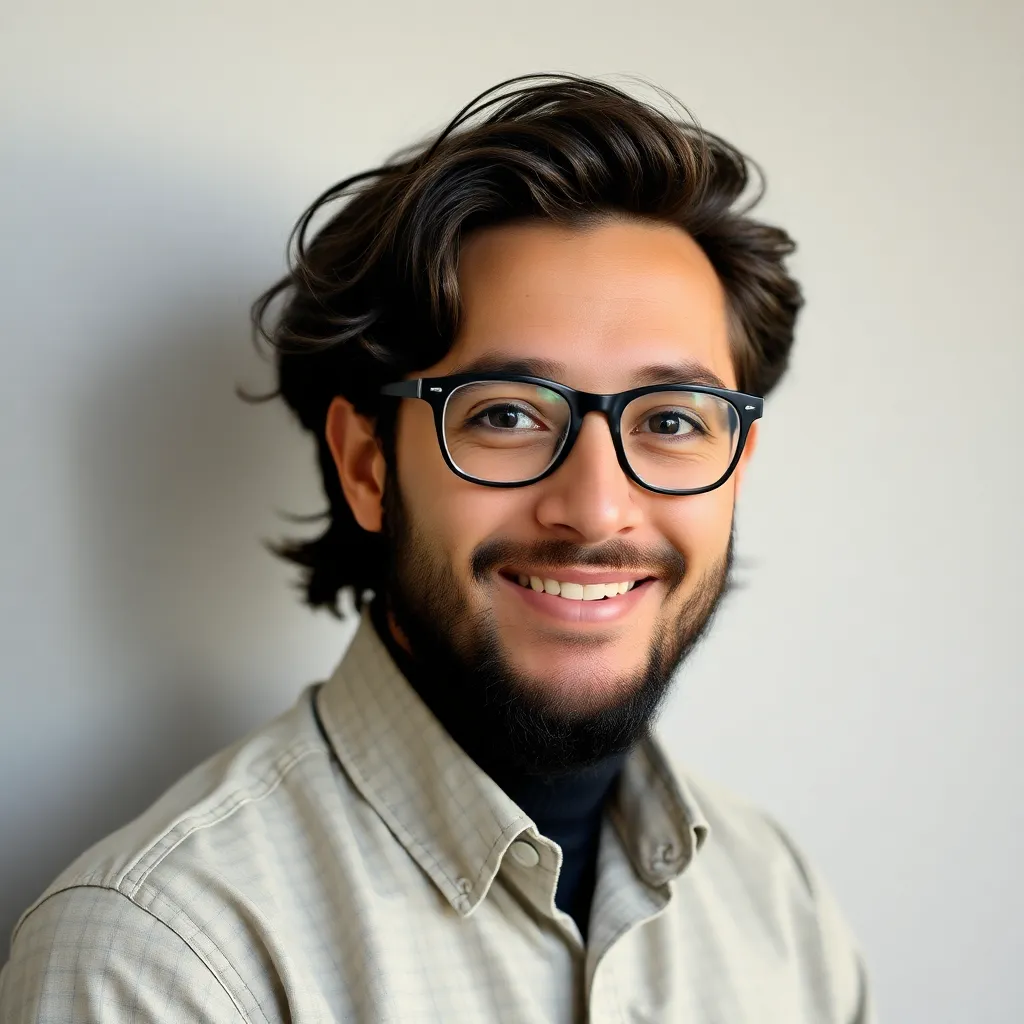
adminse
Mar 07, 2025 · 9 min read

Table of Contents
Understanding Double Gearing: A Deep Dive into its Definition, Mechanics, and Applications
What if the seemingly simple concept of gearing held the key to unlocking superior power transmission in complex machinery? Double gearing, a sophisticated mechanism employing two sets of gears, is precisely that—a powerful tool with widespread applications across diverse industries.
Editor’s Note: This article on double gearing provides a comprehensive overview of this important mechanical system, covering its definition, functionality, advantages, disadvantages, and various applications. The information presented is based on established mechanical engineering principles and industry best practices.
Why Double Gearing Matters: Relevance, Practical Applications, and Industry Significance
Double gearing is far more than a mere theoretical concept. It represents a critical advancement in mechanical engineering, enabling the efficient transmission of high torque and power at reduced speeds. This is particularly important in applications where high power output is needed, while minimizing the size and weight of components. Industries ranging from automotive and aerospace to manufacturing and robotics leverage double gearing's capabilities. The ability to achieve a high gear ratio with compact design makes double gearing a cornerstone of many high-performance and precision systems. Understanding its mechanics allows for better design, improved efficiency, and the development of innovative solutions across diverse fields.
Overview: What This Article Covers
This article will delve into the intricacies of double gearing, starting with its fundamental definition and exploring its various configurations. We will examine its advantages and disadvantages, investigate its practical applications in diverse industries, and address common misconceptions surrounding its implementation. Furthermore, we'll explore the relationship between double gearing and other mechanical components and conclude with a comprehensive FAQ section.
The Research and Effort Behind the Insights
This article is the result of extensive research, drawing upon established mechanical engineering textbooks, peer-reviewed journal articles, and industry publications. The information presented is verified through multiple sources, ensuring accuracy and reliability. The structural approach employed ensures clarity and logical progression of ideas, providing readers with a well-rounded understanding of double gearing.
Key Takeaways:
- Definition and Core Concepts: A clear definition of double gearing, outlining its fundamental principles and distinguishing it from single-stage gearing.
- Types and Configurations: An examination of various double gearing arrangements, including compound gearing and planetary gear systems.
- Advantages and Disadvantages: A balanced assessment of the benefits and drawbacks associated with double gearing, considering factors like efficiency, compactness, and cost.
- Applications Across Industries: Real-world examples illustrating the diverse applications of double gearing in various sectors.
- Challenges and Solutions: An exploration of common challenges encountered during the design and implementation of double gearing systems and strategies for mitigation.
Smooth Transition to the Core Discussion
Having established the importance and scope of our exploration, let's now embark on a detailed examination of double gearing, starting with its foundational definition.
Exploring the Key Aspects of Double Gearing
Definition and Core Concepts:
Double gearing, in its simplest form, is a power transmission system that utilizes two sets of gears in series to achieve a desired gear ratio. This contrasts with single-stage gearing, which employs only one set of gears. The primary purpose of double gearing is to significantly increase (or decrease) the rotational speed and torque of a driven shaft relative to the driving shaft. The overall gear ratio in a double gearing system is the product of the individual gear ratios of the two gear sets.
Types and Configurations:
Several configurations exist for double gearing systems, each offering distinct advantages and disadvantages. Two prominent types are:
-
Compound Gearing: In compound gearing, two or more pairs of gears are mounted on separate shafts, forming a series of gear trains. Each gear pair contributes to the overall gear ratio, leading to a high overall ratio in a compact space. The intermediate shaft allows for a change in the direction of rotation.
-
Planetary Gear Systems: Planetary gear systems represent a more complex form of double gearing, involving a central sun gear, multiple planet gears, and a ring gear. This arrangement allows for a wide range of gear ratios and can achieve high torque multiplication with significant efficiency. Planetary systems are often used in applications requiring variable speed control, such as automatic transmissions.
Advantages of Double Gearing:
- High Gear Ratio: Double gearing excels at achieving very high (or very low) gear ratios efficiently, which is critical in numerous applications.
- Compact Design: Compared to single-stage systems achieving the same gear ratio, double gearing often offers a more compact design, saving space and weight.
- Increased Torque: The high gear ratio facilitates a significant increase in torque at the output shaft, crucial for applications demanding high power.
- Improved Efficiency (in certain configurations): While friction losses are inherent, well-designed double gearing systems, especially those employing planetary gears, can achieve high overall efficiency.
Disadvantages of Double Gearing:
- Increased Complexity: The design and manufacturing of double gearing systems are more complex compared to single-stage systems, leading to higher costs.
- Higher Friction Losses (potential): The increased number of meshing gears can result in higher frictional losses if not properly designed and lubricated. Careful selection of materials and precision manufacturing are essential.
- Backlash: The cumulative backlash from multiple gear pairs can affect the precision and accuracy of the system, especially in applications requiring high positional accuracy.
Applications Across Industries:
The applications of double gearing are extensive and diverse:
- Automotive Industry: Used in vehicle transmissions (especially in heavy-duty vehicles), providing various gear ratios for different driving conditions. Double gearing systems are fundamental to automatic transmissions, enabling smooth transitions between gears.
- Aerospace Industry: Found in aircraft and spacecraft mechanisms, contributing to the precise control of actuators, rotors, and other components. The compact size and high torque multiplication are crucial for weight-sensitive applications.
- Manufacturing Industry: Used in various machinery, including lathes, milling machines, and gearboxes for power tools. They deliver the high torque required for precise machining operations.
- Robotics: Essential components in robotic arms and other mechanisms, offering the control and power needed for accurate and efficient movements.
- Wind Turbines: Used in the gearboxes of wind turbines, converting the relatively slow rotation of the turbine blades into faster rotation for efficient electricity generation.
Challenges and Solutions:
Designing and implementing double gearing systems effectively involves overcoming several challenges:
- Backlash Minimization: Careful selection of gear types, precise manufacturing tolerances, and appropriate pre-load can mitigate backlash effects.
- Lubrication and Cooling: Adequate lubrication is essential to reduce friction losses and maintain efficiency. In high-power applications, cooling systems may be necessary to prevent overheating.
- Noise Reduction: The meshing of multiple gears can generate noise. Careful gear design, precision manufacturing, and noise-dampening measures can minimize these issues.
Exploring the Connection Between Gear Material and Double Gearing
The choice of gear material significantly influences the performance and lifespan of a double gearing system. This section explores the relationship between gear material selection and double gearing effectiveness.
Key Factors to Consider:
-
Roles and Real-World Examples: Materials like steel (various grades), bronze, and polymers are used depending on the specific application's load, speed, and environmental conditions. For instance, high-strength steel alloys are typically chosen for high-torque applications in automotive transmissions. Bronze gears may be preferred where corrosion resistance is vital.
-
Risks and Mitigations: Incorrect material selection can lead to premature wear, failure, and reduced efficiency. Proper material selection involves considering factors such as hardness, strength, wear resistance, and cost-effectiveness. Finite element analysis (FEA) can aid in predicting gear performance under various load conditions.
-
Impact and Implications: The material selection directly impacts the overall gear ratio accuracy, durability, noise levels, and maintenance requirements. A well-informed choice is crucial for optimizing the performance and extending the lifespan of the double gearing system.
Conclusion: Reinforcing the Connection
The gear material selection is integral to the success of a double gearing system. By carefully considering the material properties in relation to operating conditions, designers can optimize performance and minimize risks, ultimately maximizing the benefits of double gearing.
Further Analysis: Examining Gear Manufacturing Precision in Greater Detail
Manufacturing precision is paramount in double gearing systems. Even minor deviations can lead to significant performance issues. Precise manufacturing ensures accurate meshing, minimizing backlash and maximizing efficiency.
FAQ Section: Answering Common Questions About Double Gearing
-
Q: What is the difference between double gearing and compound gearing?
- A: While often used interchangeably, compound gearing is a type of double gearing. Double gearing broadly refers to any system using two sets of gears; compound gearing specifically describes the arrangement where two gear pairs are mounted on separate shafts.
-
Q: How is the overall gear ratio calculated in a double gearing system?
- A: The overall gear ratio is calculated by multiplying the gear ratios of the individual gear sets.
-
Q: What are the common failure modes of double gearing systems?
- A: Common failure modes include gear tooth wear, pitting, breakage, and bearing failure. These can be caused by excessive loads, improper lubrication, or manufacturing defects.
-
Q: Can double gearing systems be used in reverse?
- A: Yes, depending on the specific configuration, double gearing systems can operate in both forward and reverse directions. This is often achieved through the use of idler gears or planetary gear arrangements.
-
Q: What are some design considerations for minimizing noise in double gearing systems?
- A: Design considerations for noise reduction include selecting gears with proper tooth profiles (e.g., involute), ensuring precise alignment, using appropriate materials, and incorporating noise-damping measures.
Practical Tips: Maximizing the Benefits of Double Gearing
- Proper Gear Selection: Choose gears with the appropriate tooth profile, material, and module for the intended application.
- Precision Manufacturing: Ensure that gears are manufactured to precise tolerances to minimize backlash and maximize efficiency.
- Adequate Lubrication: Use the correct type and amount of lubricant to reduce friction and wear.
- Regular Maintenance: Regular inspection and maintenance are crucial to identify and address potential problems early on.
Final Conclusion: Wrapping Up with Lasting Insights
Double gearing represents a powerful and versatile mechanism for efficient power transmission. By understanding its principles, advantages, disadvantages, and potential challenges, engineers can effectively leverage its capabilities across a broad spectrum of applications. Careful design, precise manufacturing, and appropriate material selection are key to maximizing its benefits and ensuring the longevity of these sophisticated systems. The ongoing advancements in materials science and manufacturing techniques continue to refine the efficiency, reliability, and applications of double gearing, making it a critical technology for future innovations.
Latest Posts
Related Post
Thank you for visiting our website which covers about Double Gearing Definition . We hope the information provided has been useful to you. Feel free to contact us if you have any questions or need further assistance. See you next time and don't miss to bookmark.