Cracking Definition Petroleum Refining
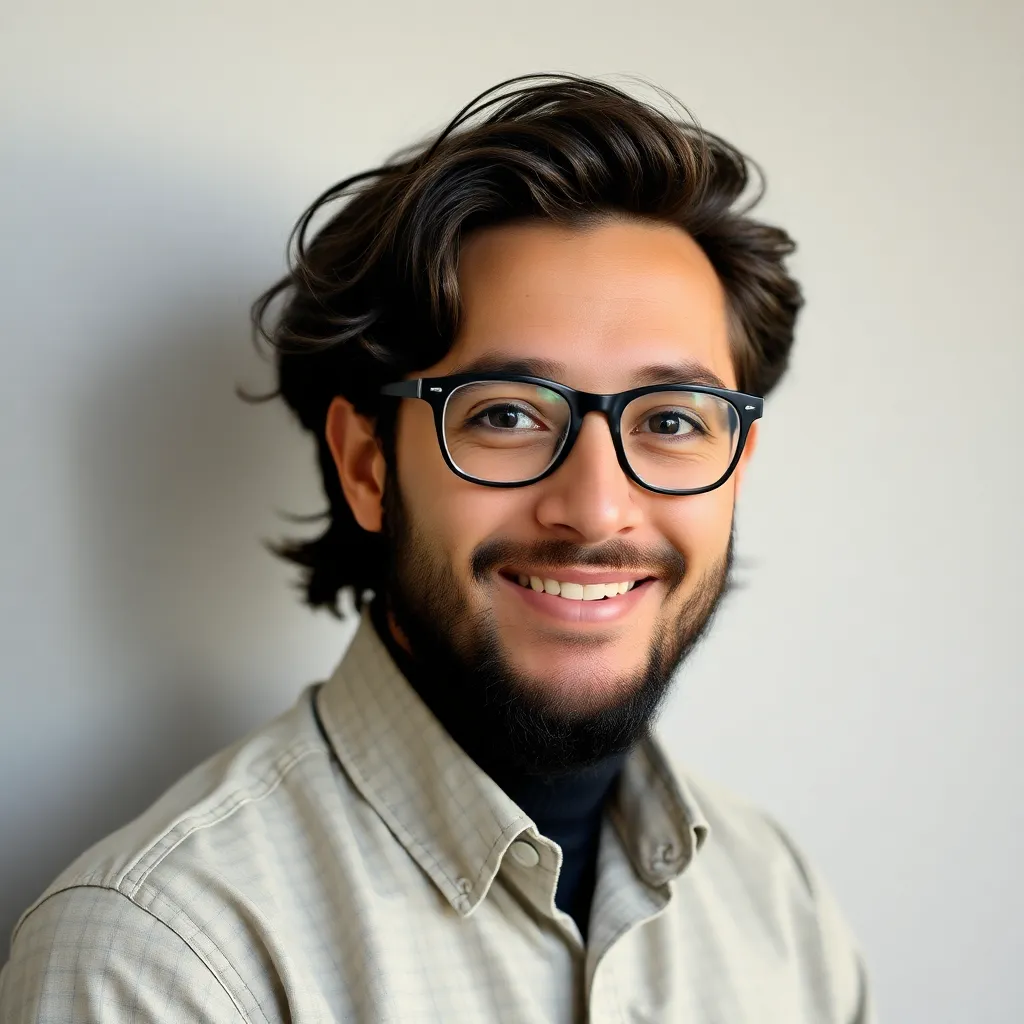
adminse
Mar 29, 2025 · 9 min read

Table of Contents
Cracking: Definition, Processes, and the Heart of Petroleum Refining
What if the future of fuel efficiency hinges on our understanding of cracking in petroleum refining? This critical process is the backbone of modern fuel production, transforming crude oil into the valuable products we rely on daily.
Editor’s Note: This article on cracking in petroleum refining provides a comprehensive overview of the various cracking processes, their applications, and their significance in the modern petrochemical industry. The information presented is current as of October 26, 2023.
Why Cracking Matters: Relevance, Practical Applications, and Industry Significance
Cracking is not merely a process within petroleum refining; it’s the fundamental transformation that converts large, complex hydrocarbon molecules found in crude oil into smaller, more valuable molecules suitable for use as fuels and petrochemicals. Without cracking, the abundance of heavy, high-boiling-point hydrocarbons in crude oil would be largely unusable. The process directly impacts the availability and affordability of gasoline, diesel, jet fuel, and a vast array of plastics, solvents, and other petrochemical products. Its importance is paramount to modern society’s energy needs and material supply chains. The efficiency and sophistication of cracking techniques directly influence the profitability and environmental impact of refineries worldwide.
Overview: What This Article Covers
This article will delve into the core aspects of cracking in petroleum refining, exploring its definition, different types (thermal and catalytic), the chemistry behind the process, and its crucial role in optimizing fuel yields and petrochemical production. It will examine the various catalysts used, the operational parameters influencing efficiency, and the ongoing advancements in cracking technology aimed at improving yields, reducing energy consumption, and minimizing environmental impact. We will also analyze the relationship between cracking and the production of valuable byproducts.
The Research and Effort Behind the Insights
This article is the result of extensive research, drawing upon reputable sources including academic journals, industry reports from organizations like the American Petroleum Institute (API), and technical publications from leading refinery equipment manufacturers. Information has been synthesized to provide a clear, concise, and accurate understanding of cracking, suitable for a broad audience with an interest in petroleum refining.
Key Takeaways:
- Definition and Core Concepts: A clear explanation of cracking and its fundamental principles.
- Thermal vs. Catalytic Cracking: A detailed comparison of these two major cracking methods.
- Catalytic Cracking Catalysts: An overview of the types of catalysts used and their impact on product selectivity.
- Process Variables and Optimization: A discussion of the parameters that influence cracking efficiency and product distribution.
- Byproduct Production and Utilization: An examination of the valuable byproducts generated during cracking.
- Future Trends in Cracking Technology: An exploration of emerging technologies aimed at improving efficiency and sustainability.
Smooth Transition to the Core Discussion:
Having established the significance of cracking in petroleum refining, let's now explore the detailed mechanisms and technological aspects of this crucial process.
Exploring the Key Aspects of Cracking
1. Definition and Core Concepts:
Cracking is a thermochemical process that breaks down large, high-molecular-weight hydrocarbon molecules (typically found in heavier fractions of crude oil like gas oil and residue) into smaller, lower-molecular-weight molecules, including gasoline, diesel, and other valuable petrochemicals. This process involves the breaking of carbon-carbon bonds (C-C) within the hydrocarbon chains, often accompanied by the formation of new carbon-carbon bonds and the rearrangement of existing ones. The result is a shift in the product distribution, increasing the yield of more desirable lighter hydrocarbons.
2. Thermal Cracking vs. Catalytic Cracking:
-
Thermal Cracking: This older method relies solely on high temperature and pressure to break down the hydrocarbon molecules. It's a relatively simpler process but less efficient and selective than catalytic cracking. Thermal cracking produces a wider range of products with a lower proportion of gasoline and a higher proportion of less desirable products like coke.
-
Catalytic Cracking: This method employs catalysts, typically zeolites, to facilitate the breaking of C-C bonds at lower temperatures and pressures than thermal cracking. Catalysts enhance the selectivity of the process, increasing the yield of desired products like gasoline and reducing the formation of coke and other undesirable byproducts. Catalytic cracking is far more efficient and widely used in modern refineries. Fluid catalytic cracking (FCC) is the most common type of catalytic cracking.
3. Fluid Catalytic Cracking (FCC): A Deeper Dive
FCC units are the workhorses of modern refineries. These complex systems utilize a finely powdered catalyst (typically a zeolite-based material) that is continuously circulated within the reactor. Heavy oil feedstock is contacted with the hot catalyst in the reactor, undergoing cracking reactions. The catalyst-oil mixture then moves to a regenerator where coke deposits are burned off, restoring the catalyst's activity. This continuous regeneration allows for sustained operation of the unit. The product vapors from the reactor are then fractionated to separate the different hydrocarbon products based on their boiling points.
4. Catalytic Cracking Catalysts:
The choice of catalyst is critical in determining the efficiency and product distribution of catalytic cracking. Zeolites are the most common catalysts due to their high surface area, pore structure, and acidic properties, which promote the desired cracking reactions. The specific composition and structure of the zeolite can be tailored to optimize the production of particular products. Promoters and stabilizers may be added to the catalyst to enhance its activity, selectivity, and longevity.
5. Process Variables and Optimization:
Several parameters influence the efficiency and product distribution of cracking processes:
- Temperature: Higher temperatures generally lead to increased cracking activity but also to increased coke formation.
- Pressure: Lower pressures favor the formation of lighter hydrocarbons.
- Catalyst-to-Oil Ratio: A higher catalyst-to-oil ratio generally leads to higher conversion rates and improved product selectivity.
- Residence Time: The length of time the feedstock spends in the reactor affects the extent of cracking.
- Feedstock Composition: The type and properties of the feedstock greatly influence the product distribution.
6. Byproduct Production and Utilization:
Cracking generates various byproducts, many of which are valuable:
- Liquefied Petroleum Gas (LPG): Used as a fuel and in petrochemical production.
- Gasoline: The primary product, used as motor fuel.
- Diesel: Used as fuel for heavy-duty vehicles and machinery.
- Coke: Used in various industrial applications, including steel production.
- Petrochemicals: Cracking is a crucial source of feedstocks for the petrochemical industry, yielding olefins (ethylene, propylene) used in the production of plastics, polymers, and other materials.
7. Future Trends in Cracking Technology:
Ongoing research focuses on improving the efficiency and sustainability of cracking processes:
- Advanced Catalysts: Development of more active, selective, and longer-lasting catalysts.
- Process Optimization: Employing advanced process control strategies to optimize product yields and minimize energy consumption.
- Integration with Other Processes: Combining cracking with other refinery processes to enhance overall efficiency and reduce waste.
- Renewable Feedstocks: Exploring the use of renewable feedstocks (e.g., biomass) in cracking processes to reduce reliance on fossil fuels.
Exploring the Connection Between Coke Formation and Cracking
Coke is an unavoidable byproduct of cracking. It's a carbonaceous material formed by the polymerization of smaller hydrocarbon molecules. While it has some industrial applications, excessive coke formation in cracking units is undesirable because it deactivates the catalyst, reduces reactor efficiency, and requires frequent regeneration.
Key Factors to Consider:
-
Roles and Real-World Examples: The rate of coke formation is highly dependent on the operating conditions (temperature, pressure, residence time) and the nature of the feedstock. High-molecular-weight feedstocks tend to produce more coke. In FCC units, coke deposition on the catalyst necessitates continuous regeneration to maintain catalytic activity.
-
Risks and Mitigations: Excessive coke formation can lead to catalyst deactivation, reduced product yield, and increased operating costs. Strategies to mitigate coke formation include optimizing operating conditions, employing advanced catalyst formulations, and using coke-resistant catalyst supports.
-
Impact and Implications: Coke formation has significant economic and environmental implications. The energy required for coke burning during regeneration contributes to the refinery's energy consumption and greenhouse gas emissions.
Conclusion: Reinforcing the Connection
The relationship between coke formation and cracking highlights the inherent trade-off between achieving high conversion rates and minimizing undesirable byproducts. Careful process optimization and the use of advanced catalyst technologies are essential for managing coke formation while maximizing the production of valuable products.
Further Analysis: Examining Coke Management in Greater Detail
Coke management in cracking units involves a combination of process control, catalyst selection, and regeneration strategies. Advanced regeneration techniques, such as improved burner design and oxygen control, can significantly enhance the efficiency of coke removal, reducing energy consumption and environmental impact.
FAQ Section: Answering Common Questions About Cracking
Q: What is the main purpose of cracking in petroleum refining?
A: The main purpose is to convert large, heavy hydrocarbon molecules from crude oil into smaller, more valuable molecules like gasoline, diesel, and petrochemicals.
Q: What are the main types of cracking?
A: The two main types are thermal cracking and catalytic cracking, with catalytic cracking being far more prevalent in modern refineries.
Q: What is the role of a catalyst in catalytic cracking?
A: The catalyst facilitates the breaking of C-C bonds at lower temperatures and pressures, increasing the efficiency and selectivity of the process.
Q: What are some of the byproducts of cracking?
A: Byproducts include LPG, gasoline, diesel, coke, and various petrochemicals.
Q: What are some of the future trends in cracking technology?
A: Future trends include developing more advanced catalysts, optimizing process conditions, integrating cracking with other processes, and exploring the use of renewable feedstocks.
Practical Tips: Maximizing the Benefits of Cracking
- Optimize Feedstock Selection: Choose feedstocks that are well-suited for the specific cracking process and desired product distribution.
- Monitor and Control Process Parameters: Closely monitor temperature, pressure, residence time, and catalyst-to-oil ratio to optimize performance and minimize coke formation.
- Invest in Advanced Catalyst Technologies: Employing catalysts with enhanced activity, selectivity, and coke resistance can significantly improve efficiency.
- Implement Robust Regeneration Strategies: Efficient coke burning during regeneration is crucial for maintaining catalyst activity and minimizing energy consumption.
Final Conclusion: Wrapping Up with Lasting Insights
Cracking is the cornerstone of modern petroleum refining, enabling the transformation of crude oil into the fuels and petrochemicals that power our world. By understanding the intricate details of this process and continuously developing more efficient and sustainable cracking technologies, the industry can continue to meet global energy demands while minimizing its environmental impact. The ongoing quest for enhanced efficiency, selectivity, and environmentally benign approaches will continue to shape the future of cracking and petroleum refining for years to come.
Latest Posts
Related Post
Thank you for visiting our website which covers about Cracking Definition Petroleum Refining . We hope the information provided has been useful to you. Feel free to contact us if you have any questions or need further assistance. See you next time and don't miss to bookmark.